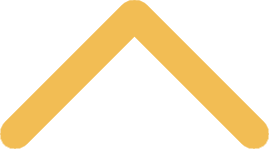
Safety: Aerial Lifts/Powered Platforms
Applies to: All staff using any aerial lift equipment.
Purpose: It is the purpose of this program to prevent the improper and unsafe use of Aerial Lifts that can potentially result in serious injury or death. Ensure that only trained, authorized and certified personnel will operate and understand the limitations of aerial lifts. Ensure that all employees are following the rules of safe operation and are maintaining the lift in a safe operating condition.
Policy Owner: Human Resources
Revision Dates: August 2024
Policy
Departments
Each operating division is responsible for the proper training and compliance with the criteria set forth in this policy.
Human Resources
- Overall program coordinator.
- Maintain all training records.
- Audit divisions for compliance with this policy.
Departmental Managers
- Responsible for the implementation and enforcement of the Aerial Lift policy.
- Provide Human Resources with an updated listing of trained personnel.
- Responsible for ensuring that only trained operators, operating safely, are allowed to operate aerial lifts.
- Ensure that all equipment is maintained in good working order.
- Schedule all preventive maintenance in accordance with the manufacturer’s recommendation (keep records for 5 years).
- Ensure that any operators have received hands on training from a qualified instructor.
Employees (Operators)
- Responsible for inspecting the lift before each use and completing an inspection list. Trained and authorized personnel must have a complete grasp of the use, limitations and safe operations as they pertain to the aerial lift they operate.
- Responsible for reporting any defects of the lift to the departmental manager immediately.
- Proper PPE (hard hats, safety glasses, fall protection when using all lifts) must be worn while operating lifts.
- Must adhere to all safety rules, procedures, and regulations.
- Will be retrained if the type of aerial lift changes or if the employee is not operating a lift properly. Refresher training is required at least once every three years.
Procedures
Pre-Operational Inspection
A pre-operational inspection (or frequent inspection) must be done prior to operating the lift.
- Vehicle Inspection
- Oil level
- Hydraulic oil level
- Fuel level
- Check the lift and surrounding area for leaks
- Coolant level
- Tire pressure and condition of wheels and tires
- Battery and charger
- Ground control switches
- Operational Check
- Horn
- Gauges
- Brakes
- Lights
- Steering
- Attachments or accessories
- Backup alarm or warning buzzer
- Warning lights
- Platform Lift Equipment Inspection
- Lift and travel controls and switches
- Placards, decals and control ID labels
- Handrails, guardrails and safety chains
- Platform deck and toe boards
- Steering
- Attachments or accessories
- Backup alarm or warning buzzer
- Warning lights
If the inspection reveals a problem with the aerial lift, the unit must be placed (tagged) out of service until the repairs have been made and the unit is operating safely.
Personnel
- Person in Charge: the operator will be assigned responsibility for the operations of the aerial lift. Before beginning operations, a visual inspection of the unit shall be made to insure it is in safe operating condition.
- Crew: It is recommended that at least two people work with an aerial lift. The crew would consist of a qualified person in the bucket and one person on the ground that is trained and qualified in the emergency letdown procedure. If operating alone, or without someone on the ground, the operator is required to carry a working two-way radio or cell phone in the bucket.
- Qualified Workers: All work from an aerial lift shall be performed by employees trained and qualified to do such work. Qualified employees will be familiar with the operation of the lift controls, maneuverability, and load carrying capabilities.
Moving the Lift
- Make sure there is adequate clearance for exposed equipment above the cab of the lift. Watch for on the ground hazards such as uneven ground and debris.
- While moving a lift, the booms and buckets shall be locked into the cradled position and the outriggers (if any) shall be retracted. Employees are not permitted to ride in the bucket while the truck is moving.
- Under no conditions shall the aerial lift be moved with the booms elevated from the cradled position or with employees in the bucket.
- Do not use lifts of any kind for pushing or pulling other objects.
- Drive slowly and carefully. Use a second person to assist on the ground.
Operating a Lift
- Always close lift platform chains or doors.
- Set outriggers, braces, brakes and/or wheel chocks, even if working on level ground.
- Be sure the ground where you are operating the lift will adequately support the machine.
- Stand on the floor of the bucket or lift platform. DO NOT climb on or lean over guardrails.
- Never sit or stand on the lip of the bucket or place anything across the top of the bucket to gain additional working height.
- While operating from the bucket, always face the direction in which you are moving and be aware of existing conditions and equipment, conductors, and other obstructions.
- Do not exceed manufacturer’s load-capacity limits (including weight of tools, etc.)
- Never modify equipment without written approval from the manufacturer.
- If working near traffic, set up cones and signs.
- If working outside, do not operate if wind is greater than 15 mph.
- To prevent electrocutions, workers must stay at least 10 feet away from overhead power lines.
- To prevent falls, OSHA requires either a full-body harness on bucket trucks or boom-supported lifts. Tip over hazards:
- Do not drive or position lifts near the edge of loading dock drop offs or holes
- Do not raise the platform on uneven or soft surface
- Do not raise the platform in windy conditions
- Do not use the platform as a crane
- Do not place or attach overhanging loads to any part of the platform
- Do not place ladders or scaffolds in the platform or against any part of the lift
- Tie off must be to the designated points on the bucket or the boom designated from the manufacturer.
Contractors
Contractors working on St. Norbert College property will need to sign a Waiver of Liability to be allowed to use St. Norbert College leased or owned Aerial Lifts to perform work. Print the waiver form, fill in the blanks on the form, and have it signed prior to allowing the use of the Lift. All releases must be kept on file with the department manager for a period of 3 years which is the statute of limitation for filing a lawsuit in the State of Wisconsin. Should an incident occur, please report it to the SNC Risk and Property Management Director as soon as possible, along with a copy of the signed waiver of the involved person(s). Contractors must use their own equipment unless this waiver is signed.
Program Review & Update
This policy shall be reviewed and updated on an annual basis or sooner if necessary.
Policy
Departments
Each operating division is responsible for the proper training and compliance with the criteria set forth in this policy.
Human Resources
- Overall program coordinator.
- Maintain all training records.
- Audit divisions for compliance with this policy.
Departmental Managers
- Responsible for the implementation and enforcement of the Aerial Lift policy.
- Provide Human Resources with an updated listing of trained personnel.
- Responsible for ensuring that only trained operators, operating safely, are allowed to operate aerial lifts.
- Ensure that all equipment is maintained in good working order.
- Schedule all preventive maintenance in accordance with the manufacturer’s recommendation (keep records for 5 years).
- Ensure that any operators have received hands on training from a qualified instructor.
Employees (Operators)
- Responsible for inspecting the lift before each use and completing an inspection list. Trained and authorized personnel must have a complete grasp of the use, limitations and safe operations as they pertain to the aerial lift they operate.
- Responsible for reporting any defects of the lift to the departmental manager immediately.
- Proper PPE (hard hats, safety glasses, fall protection when using all lifts) must be worn while operating lifts.
- Must adhere to all safety rules, procedures, and regulations.
- Will be retrained if the type of aerial lift changes or if the employee is not operating a lift properly. Refresher training is required at least once every three years.
Procedures
Pre-Operational Inspection
A pre-operational inspection (or frequent inspection) must be done prior to operating the lift.
- Vehicle Inspection
- Oil level
- Hydraulic oil level
- Fuel level
- Check the lift and surrounding area for leaks
- Coolant level
- Tire pressure and condition of wheels and tires
- Battery and charger
- Ground control switches
- Operational Check
- Horn
- Gauges
- Brakes
- Lights
- Steering
- Attachments or accessories
- Backup alarm or warning buzzer
- Warning lights
- Platform Lift Equipment Inspection
- Lift and travel controls and switches
- Placards, decals and control ID labels
- Handrails, guardrails and safety chains
- Platform deck and toe boards
- Steering
- Attachments or accessories
- Backup alarm or warning buzzer
- Warning lights
If the inspection reveals a problem with the aerial lift, the unit must be placed (tagged) out of service until the repairs have been made and the unit is operating safely.
Personnel
- Person in Charge: the operator will be assigned responsibility for the operations of the aerial lift. Before beginning operations, a visual inspection of the unit shall be made to insure it is in safe operating condition.
- Crew: It is recommended that at least two people work with an aerial lift. The crew would consist of a qualified person in the bucket and one person on the ground that is trained and qualified in the emergency letdown procedure. If operating alone, or without someone on the ground, the operator is required to carry a working two-way radio or cell phone in the bucket.
- Qualified Workers: All work from an aerial lift shall be performed by employees trained and qualified to do such work. Qualified employees will be familiar with the operation of the lift controls, maneuverability, and load carrying capabilities.
Moving the Lift
- Make sure there is adequate clearance for exposed equipment above the cab of the lift. Watch for on the ground hazards such as uneven ground and debris.
- While moving a lift, the booms and buckets shall be locked into the cradled position and the outriggers (if any) shall be retracted. Employees are not permitted to ride in the bucket while the truck is moving.
- Under no conditions shall the aerial lift be moved with the booms elevated from the cradled position or with employees in the bucket.
- Do not use lifts of any kind for pushing or pulling other objects.
- Drive slowly and carefully. Use a second person to assist on the ground.
Operating a Lift
- Always close lift platform chains or doors.
- Set outriggers, braces, brakes and/or wheel chocks, even if working on level ground.
- Be sure the ground where you are operating the lift will adequately support the machine.
- Stand on the floor of the bucket or lift platform. DO NOT climb on or lean over guardrails.
- Never sit or stand on the lip of the bucket or place anything across the top of the bucket to gain additional working height.
- While operating from the bucket, always face the direction in which you are moving and be aware of existing conditions and equipment, conductors, and other obstructions.
- Do not exceed manufacturer’s load-capacity limits (including weight of tools, etc.)
- Never modify equipment without written approval from the manufacturer.
- If working near traffic, set up cones and signs.
- If working outside, do not operate if wind is greater than 15 mph.
- To prevent electrocutions, workers must stay at least 10 feet away from overhead power lines.
- To prevent falls, OSHA requires either a full-body harness on bucket trucks or boom-supported lifts. Tip over hazards:
- Do not drive or position lifts near the edge of loading dock drop offs or holes
- Do not raise the platform on uneven or soft surface
- Do not raise the platform in windy conditions
- Do not use the platform as a crane
- Do not place or attach overhanging loads to any part of the platform
- Do not place ladders or scaffolds in the platform or against any part of the lift
- Tie off must be to the designated points on the bucket or the boom designated from the manufacturer.
Contractors
Contractors working on St. Norbert College property will need to sign a Waiver of Liability to be allowed to use St. Norbert College leased or owned Aerial Lifts to perform work. Print the waiver form, fill in the blanks on the form, and have it signed prior to allowing the use of the Lift. All releases must be kept on file with the department manager for a period of 3 years which is the statute of limitation for filing a lawsuit in the State of Wisconsin. Should an incident occur, please report it to the SNC Risk and Property Management Director as soon as possible, along with a copy of the signed waiver of the involved person(s). Contractors must use their own equipment unless this waiver is signed.
Program Review & Update
This policy shall be reviewed and updated on an annual basis or sooner if necessary.
Contact Us
Location
Our office is located on First Street in the Garden Level (lower level) of Main Hall in De Pere, Wis.
Campus Map
Hours of Operation
Monday-Friday
8 a.m.-4:30 p.m.
Phone: 920-403-3211
Fax: 920-403-3983
Email: hr@snc.edu