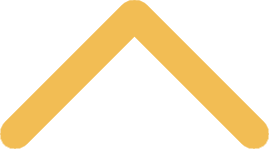
Safety: Cranes, Hoists, Slings, and Rigging
Applies to: All faculty, staff, and any contractors working on SNC property
Purpose: Cranes, hoists, and rigging devices are used at St. Norbert College for lifting and moving materials. This policy applies to all operations at St. Norbert College that involve the use of cranes, rigging devices, and hoists used or attached to a building.
Policy Owner: Human Resources
Revision Dates: December 2022
Policy
RESPONSIBILITIES
Departments
Each department is responsible for compliance with the criteria set forth in this program. They must ensure that all elements of this program and related procedures are implemented and followed.
Sr. Benefits and Safety Specialist
- Review changes in operations and keep current with new processes and/or facilities within the College and identify new Crane, Hoist, Slings & Rigging requirements when needed.
- Work with managers and coordinate efforts to analyze, minimize occupational exposures.
- Document and maintain training records.
- Ensuring that employees under their supervision receive the required training from supplier and/or are certified and/or licensed to operate and maintain the cranes, hoists, slings and rigging in their areas.
- Providing initial training for any employees that may use this equipment by a competent person.
- Ensuring that hoisting equipment is visually inspected before use by a responsible individual and that rigging equipment is inspected annually by a professional.
- Maintain written records of inspections and tests and keep them on file.
- Inspecting and load testing cranes and hoists following modification or extensive repairs owned by St. Norbert College are only to be done by a professional.
- Maintaining all manuals in reference to College owned cranes and hoists.
Employees
- Operating hoisting equipment safely.
- Conducting functional tests prior to using the equipment.
- Selecting and using rigging equipment appropriately.
- Proficient in the inspection of all equipment including the slings and documenting those inspections.
Crane and Hoist Operators - To be competent as a Crane and Hoist Operator, the candidate shall have received an articulable level of instruction or experience.
Procedures
CRANE AND HOIST SAFETY DESIGN REQUIREMENTS
The design of all commercial cranes and hoists shall comply with the requirements of ASME/ANSI B30 standards and Crane Manufacturers’ Association of America standards (CMAA-70 and CMAA-74). All Crane and Hoist Lifting equipment should be installed and approved by a professional.
The lifting capacity of the crane must be prominently labeled on the crane. The hoisting devices (i.e. chains, hooks, etc.) must also be labeled and match the lifting capacity of the crane. Any lifting hooks must be equipped with a proper working safety latch to prevent the load from falling off the hook.
GENERAL SAFETY RULES - Operators shall comply with the following rules while operating the cranes and hoists:
- Do not engage in any practice that will divert your attention while operating the cranes.
- Respond to signals only from the person who is directing the lift, or any appointed signal person. Obey a stop signal at all times, no matter who gives it.
- Do not move a load over people. People shall not be placed in jeopardy by being under a suspended load. Also, do not work under a suspended load unless the load is supported by blocks, jacks, or a solid footing that will safely support the entire weight. Have a crane or hoist operator remain at the controls or lock open and tag the main electrical disconnect switch.
- If spring-loaded reels are provided to lift pendants, clear off the work area, then ease the pendant up into a stop to prevent damaging the wire.
- Avoid side pulls. These can cause the hoist rope to slip out of the drum groove, damaging the rope or destabilizing the crane or hoist. Side loading also over stresses lifting devices such as straps, shackles, and lifting points to the point of failing.
- To prevent shock loading, avoid sudden stops or starts. Shock loading can occur when a suspended load is accelerated or decelerated, and can overload the crane or hoist. When completing an upward or downward motion, ease the load slowly to a stop.
- Before using equipment, operators shall do the following steps before making lifts with any crane or hoist:
- Perform the Crane and Hoist Checklist from manufacturer pamphlet.
- Lock out and tag for repair any crane or hoist that fails any of the above tests and inform the manager.
MOVING A LOAD
- Center hook over the load to keep the cable or chain from slipping out of the drum grooves and overlapping, and to prevent the load from swinging when it is lifted. (For Cable Hoists) Inspect the drum to verify that the cable is in the grooves.
- Use a tagline when loads must traverse long distances or must otherwise be controlled. Manila rope may be used for taglines.
- Plan and check the travel path to avoid personnel and obstructions.
- Lift the load only high enough to clear the tallest obstruction in the travel path.
- Start and stop slowly.
- Land the load when the move is finished. Choose a safe landing.
- Never leave suspended loads unattended. In an emergency where the crane or hoist has become inoperative, if a load must be left suspended, barricade and post signs in the surrounding area, under the load, and on all four sides. Lock open and tag the crane or hoist main electrical disconnect switch.
PARKING A CRANE OR HOIST
- Remove all slings and accessories from the hook. Return the rigging device to the designated storage areas.
- Raise the hook at least 7 feet above the floor.
- Store the pendant away from aisles and work areas.
- Place the emergency stop switch (or push button) in the OFF position.
SLINGS & RIGGING
- PERFORMANCE CHARACTERISTICS OF NYLON Nylon is a popular and general purpose synthetic fiber which is unaffected by common grease and oil. Nylon slings are not suitable for use with acids and bleaching agents. Exposure can result in degradation from none to total. Dilute acids, such as hydrochloric and sulfuric in 10% concentration at room temperature cause a significant loss in strength in just 10 hours.
- Nylon products lose 15% of their workload when wet. The acceptable temperature exposure range is -40°F to a maximum of 194°F. Stretch at work load limit is approximately 6 – 8%. All nylon webbing will shrink overtime as a result of the weave configuration.
- SLING-TO-LOAD ANGLE - Slings with adequate workload limits to handle the “scale” weight of the load have catastrophically failed because of an inadequate consideration of the sling angle and the increased tension. Any load rigged in a hitch that is not vertical, develops increased tension on the sling. When selecting a sling, always consider the sling-to-load angle (horizontal angle) and the tension that will be applied to the sling.
- SLING-TO-LOAD ANGLE
Angle “A” Degrees |
Loss Factor |
Angle “A” Degrees |
Loss Factor |
90 |
1.000 |
55 |
.8192 |
85 |
.9962 |
50 |
.7660 |
80 |
.9848 |
45 |
.7071 |
75 |
.9659 |
40 |
.6428 |
70 |
.9397 |
35 |
.5736 |
65 |
.9063 |
30 |
.5000 |
60 |
.8660 |
25 |
.4226 |
Sling angles of less than 45° should not be used, unless approved by a qualified person
ENVIRONMENTAL CONSIDERATIONS
- WATER - When nylon products are wet they experience a 15% reduction in strength.
- ULTRAVIOLET (UV) LIGHT:
- Can affect the strength of synthetic webbing slings in varying degrees ranging from slight to total degradation
- Factors which affect the degree of strength loss are the length of continuous exposure time, sling construction, design and other environmental factors such as weather conditions, elevation and geographical location. Loss of strength for nylon slings can be 40 to 60% after exposure for periods ranging from 12 to 36 months.
- Visual indicators of UV degradation are a bleaching out of the sling color, increased stiffness of the sling material and the appearance of abrasion in areas not normally in contact with the load.
- Slings that are subject to continuous exposure to UV light should be proof tested to two times the work load limit, semi-annually, or more frequently depending on the severity of exposure.
- TEMPERATURE - Should never be used at temperatures in excess of 194°F. Cold temperature exposure to -40°F does not affect the strength of the synthetic sling.
- STORAGE:
- Store slings in a cool, dry, dark location, free of mechanical and environmental damage.
- The storage location should be ventilated and not exposed to heat sources, weld splatter, dust or grit and splinters from grinding.
- FOREIGN MATERIAL - Metal chips, weld spatter or heavy grit can damage a sling both externally and internally.
- CHEMICAL
- Chemically active environments – including those with a combustible dust that can be corrosive - can affect the strength of synthetic products in varying degrees ranging from moderate to total degradation.
- Before slings are used the chemical compatibility between the sling components and the environment must be considered – consult the sling manufacturer.
- OTHER POINTS TO REMEMBER
- Power or pressure washing can force residue inside the web fibers. The foreign material can cause internal yarn and fiber damage.
- Aluminum hardware is severely degraded by alkali, caustic and acidic environments. Aluminum hardware should never be exposed to chlorine environments or cleaned with chlorine based solutions. Steel hardware is not impervious to these elements – chemical and environmental compatibility must be assessed and suitability determined by the user.
SLING INSPECTIONS – THREE TYPES
- INITIAL
- This inspection is done when the sling is brand new - before the sling is used
- The inspection is done by an authorized person to ensure the sling is in the expected condition and to ensure that the correct sling is being used for the load
- Per the American Society of Mechanical Engineers “prior to use, all new, altered, modified or repaired slings shall be inspected by a designated person to verify compliance to all applicable standards.”
- FREQUENT
- This inspection should be done by the person handling the sling, before every use.
- The sling should be thoroughly examined and immediately removed from service if any damage is detected. Per OSHA, “each day before being used, the sling and all fastenings and attachments shall be inspected for damage and defects by a competent person designated by the employer.”
- PERIODIC
- This inspection is done at regular intervals and may be performed by a third party. The interval is based on the frequency of use, severity of the service conditions and information derived through the inspection process.
- Periodic inspection intervals shall not exceed one year intervals.
- ASME stated that guidelines for the inspection time intervals are as follows:
- Normal Service – Yearly
- Severe Service – Monthly or Quarterly
- Special Service – As recommended by a qualified person
REMOVAL FROM SERVICE CRITERIAL - Per OSHA 1910.184 – Synthetic slings shall be immediately removed from service if any of the following conditions are present:
- Acid or caustic burns
- Melting or charring on any art of the sling surface
- Snags, punctures, tears or cuts
- Broken or worn stitches
- Distortion of fittings
ASME B30.9 – Adds the following to the list from OSHA:
- Missing or illegible sling identification - must have
- name or trademark of manufacturer
- code number or stock number
- rated loads for the type of hitch used and the angle upon which it Is based
- The type of synthetic material
- Holes, tears, cuts or snags
- Broken or worn stitching in the load bearing splices
- Excessive abrasive wear
- Knots in any part of the sling
- Discoloration and brittle or stiff areas on any part of the sling
- Fittings that are pitted, corroded, cracked, bent, twisted, gouged or broken
“MINOR DAMAGE” - A brand new 3” wide nylon sling is expected to have a vertical load limit of 4800 lbs. with a 24,000 lb. (or higher) breaking strength. Now let’s look at what happens to the breaking strength of the sling when “minor damage” occurs:
- If the sling would receive a 1/8” cut the breaking strength drops to approximately 22,150 lbs.
- With a 1/4” cut the breaking of the sling drops to approximately 18,000 lbs.
- And with a cut of 3/8” the breaking strength of the sling drops to approximately 15,500 lbs. (that’s a loss of 35% of its breaking strength)
INSPECTING SLINGS - An inspection needs to be done before each use and only takes a few minutes if done properly.
- When inspecting the sling, twist and bend the sling in all directions – small cuts and abrasions can be almost invisible.
- When bending back the sling you may notice colored warning threads (most likely red in color) if you see red the sling must be taken out of service and replaced.
- These are a good indication that the sling has been damaged and the lifting capability compromised.
- Don’t rely on the warning threads because a sling can be compromised without the threads showing.
- If the warning threads are visible, frayed, or broken take the sling out of service immediately.
- Using your hands, start at one end of the sling and bend and twist the sling. Use your hands to feel any imperfections in the sling and look closely at the sling to see if anything unusual shows up.
- Check for any parts of the sling that has been elongated – especially the end loops (eyes) of the sling. A sling with elongated eyes has probably been used for a long time or has not been used properly or has been overloaded.
- If there is any part of a sling that is discolored, rough and stiff feeling or you can’t bend it over or twist it, that sling should be taken out of service immediately.
- Look for abrasions or scuffs, burns, cuts, unraveling, snags, punctures, broken stitching, UV degradation, embedded materials, melting, charring or knots – all of which can greatly reduce the slings load limit, and take the sling out of service immediately.
- When a sling is taken out of service it should be destroyed. St. Norbert College employees are not trained or authorized to repair a sling for reuse.
- When new slings are received, they should be inspected and cataloged and given a number designation in order to track the inspections and condition of the slings. The number designation should be written on the attached label or tag – not on the sling itself.
GENERAL RIGGING SAFETY REQUIREMENTS
Only select rigging equipment that is in good condition. All rigging equipment shall be inspected and recorded monthly; defective equipment is to be removed from service and destroyed to prevent inadvertent reuse. The load capacity limits shall be stamped or affixed to all rigging components. If there is no load capacity to be found on straps or wire rope then it’s not to be used and must be taken out of service.
An inspection checklist is provided so we are able to check rigging equipment monthly. St. Norbert College policy requires slings be rejected or destroyed if they do not meet the criteria noted on the checklist.
RIGGING A LOAD
Do the following when rigging a load:
- Determine the weight of the load. Do not guess.
- Determine the proper size for slings and components.
- Make sure that shackle pins and shouldered eye bolts are installed in accordance with the manufacturer’s recommendations.
- Make sure that ordinary eye bolts are threaded in at least 1.5 times the bolt diameter.
- Use safety hoist rings (swivel eyes) as a preferred substitute for eye bolts wherever possible.
- Pad sharp edges to protect slings. Remember that machinery foundations or angle-iron edges may not feel sharp to the touch but could cut into rigging when under several tons of load. Wood, tire rubber, or other pliable materials may be suitable for padding.
- Do not use slings, eye bolts, shackles, or hooks that have been cut, welded, or brazed.
- Install wire-rope clips with the base only on the live end and the U-bolt only on the dead end. Follow the manufacturer’s recommendations for the spacing for each specific wire size.
- Determine the center of gravity and balance the load before moving it.
- Initially lift the load only a few inches to test the rigging and balance.
SLING HITCHES
Slings carry their loads in one of three primary hitches and depending upon which hitch is used, it can affect the primary load limit of the sling. Most slings can be used for any of the three hitches but there are some slings that can only be used for a certain type of hitch. It is important to check the manufacturer’s recommendations to ensure you are using the proper sling for the desired hitch.
Slings have the largest work load limit when used in a basket hitch. The work load limit of a vertical hitch is 50% of the basket hitch. The same sling would be assigned a different work load limit for the choker hitch with a work load limit that is a maximum of 80% of the vertical work load limit (per ASME recommendation).
MECHANICAL AND OPERATIONAL CONSIDERATIONS
- Remember that work load limits and break strengths that are published by the manufacturer apply to only new and unused slings, assemblies and hardware. The numbers can go down depending upon the use and condition of the sling.
- Working load limits are also based on a moderately dynamic lifting or pulling operation. Instantaneous changes (drops or sudden pick ups) in excess of 10% of the workload constitute hazardous shock loading and the working load limits as stated, do not apply.
- Do not accelerate or decelerate the load too fast. The “G” force on a 1000 lbs. load dropped 3 feet could surpass the ultimate strength of the sling. A load picked up too fast can develop a stretch/friction/surface heat that will surpass the melting temperature of the sling.
- Wide body cargo and attached eye cargo slings are for use in Basket Hitches only. Hose handling, pipe lifting slings with quick disconnect and remote release slings are for use in Choker Hitches only.
WEAR PROTECTION - Synthetic slings can be damaged, abraded or cut as tension and compression between the sling, the connection points and the load develops. The edge of the load need not be “razor” sharp to damage the sling. Below are some tips for protection the slings from wear either from the load or from the environment:
- Load edges in contact with the sling must be “padded” with materials of sufficient thickness or strength to prevent sling damage. The protection must be installed and evaluated for suitability by raising the load slightly and then lowering the load for an inspection of the sling and the protection devices.
- Wear protection may not prevent cutting or other forms of sling damage. Keep personnel away from the load and they should never be under the load.
- Slings shall not be dragged on the ground, floor or over abrasive surfaces. Slings shall not be pulled from under loads when the load is resting on the sling. If possible place blocks on the ground and lower the load onto the blocks – this will allow for easy sling removal and no potential damage. Do not run over slings with trucks or other equipment.
CRANE OVERLOADING - Cranes or hoists shall not be loaded beyond their rated capacity for normal operations. Any crane or hoist suspected of having been overloaded shall be removed from service by locking open and tagging the main disconnect switch. Additionally, overloaded cranes shall be inspected, repaired, load tested, and approved by a professional before being returned to service.
- WORKING AT HEIGHTS ON CRANES OR HOISTS
- Any conducting maintenance or repair on cranes or hoists at heights greater than 6 feet shall use fall protection. Fall protection should also be considered for heights less than 6 feet. Fall protection includes safety harnesses that are fitted with a lifeline and securely attached to a structural member of the crane or building.
- Use of crane as work platform should only be considered when conventional means of reaching an elevated worksite are hazardous or not possible. Workers shall not ride a moving bridge crane.
- HAND SIGNALS - Signals to the operator shall be in accordance with the standard hand signals unless voice communications equipment (telephone, radio, or equivalent) is used signals shall be visible or audible at all times. Some special operations may require addition to or modification of the basic signals. For all such cases, these special signals shall be agreed upon and thoroughly understood by both the person giving the signals and the operator, and shall not be in conflict with the standard signals.
- INSPECTION, MAINTENANCE, AND TESTING - All tests and inspections shall be conducted in accordance with the manufacturer’s recommendations.
- ANNUAL INSPECTIONS - The manager will schedule an annual preventive maintenance (PM) and/or annual inspections of all cranes and hoists own by St. Norbert College. The annual PM and inspection must be done by a professional and all documentation must be kept on record. A copy should be retained by the department and a copy.
- LOAD TESTING - If a crane has known to be overloaded of its capacity or has had any modifications done to it, it will have to be load tested. If load testing is necessary it will only be done by a professional. A copy should be retained by the department.
RECORDS
Managers are responsible to maintain all records for St. Norbert College owned cranes, hoist, slings, and other rigging equipment.
PROGRAM REVIEW AND UPDATE - This policy shall be reviewed and updated on an annual basis or sooner if necessary.
Policy
RESPONSIBILITIES
Departments
Each department is responsible for compliance with the criteria set forth in this program. They must ensure that all elements of this program and related procedures are implemented and followed.
Sr. Benefits and Safety Specialist
- Review changes in operations and keep current with new processes and/or facilities within the College and identify new Crane, Hoist, Slings & Rigging requirements when needed.
- Work with managers and coordinate efforts to analyze, minimize occupational exposures.
- Document and maintain training records.
- Ensuring that employees under their supervision receive the required training from supplier and/or are certified and/or licensed to operate and maintain the cranes, hoists, slings and rigging in their areas.
- Providing initial training for any employees that may use this equipment by a competent person.
- Ensuring that hoisting equipment is visually inspected before use by a responsible individual and that rigging equipment is inspected annually by a professional.
- Maintain written records of inspections and tests and keep them on file.
- Inspecting and load testing cranes and hoists following modification or extensive repairs owned by St. Norbert College are only to be done by a professional.
- Maintaining all manuals in reference to College owned cranes and hoists.
Employees
- Operating hoisting equipment safely.
- Conducting functional tests prior to using the equipment.
- Selecting and using rigging equipment appropriately.
- Proficient in the inspection of all equipment including the slings and documenting those inspections.
Crane and Hoist Operators - To be competent as a Crane and Hoist Operator, the candidate shall have received an articulable level of instruction or experience.
Procedures
CRANE AND HOIST SAFETY DESIGN REQUIREMENTS
The design of all commercial cranes and hoists shall comply with the requirements of ASME/ANSI B30 standards and Crane Manufacturers’ Association of America standards (CMAA-70 and CMAA-74). All Crane and Hoist Lifting equipment should be installed and approved by a professional.
The lifting capacity of the crane must be prominently labeled on the crane. The hoisting devices (i.e. chains, hooks, etc.) must also be labeled and match the lifting capacity of the crane. Any lifting hooks must be equipped with a proper working safety latch to prevent the load from falling off the hook.
GENERAL SAFETY RULES - Operators shall comply with the following rules while operating the cranes and hoists:
- Do not engage in any practice that will divert your attention while operating the cranes.
- Respond to signals only from the person who is directing the lift, or any appointed signal person. Obey a stop signal at all times, no matter who gives it.
- Do not move a load over people. People shall not be placed in jeopardy by being under a suspended load. Also, do not work under a suspended load unless the load is supported by blocks, jacks, or a solid footing that will safely support the entire weight. Have a crane or hoist operator remain at the controls or lock open and tag the main electrical disconnect switch.
- If spring-loaded reels are provided to lift pendants, clear off the work area, then ease the pendant up into a stop to prevent damaging the wire.
- Avoid side pulls. These can cause the hoist rope to slip out of the drum groove, damaging the rope or destabilizing the crane or hoist. Side loading also over stresses lifting devices such as straps, shackles, and lifting points to the point of failing.
- To prevent shock loading, avoid sudden stops or starts. Shock loading can occur when a suspended load is accelerated or decelerated, and can overload the crane or hoist. When completing an upward or downward motion, ease the load slowly to a stop.
- Before using equipment, operators shall do the following steps before making lifts with any crane or hoist:
- Perform the Crane and Hoist Checklist from manufacturer pamphlet.
- Lock out and tag for repair any crane or hoist that fails any of the above tests and inform the manager.
MOVING A LOAD
- Center hook over the load to keep the cable or chain from slipping out of the drum grooves and overlapping, and to prevent the load from swinging when it is lifted. (For Cable Hoists) Inspect the drum to verify that the cable is in the grooves.
- Use a tagline when loads must traverse long distances or must otherwise be controlled. Manila rope may be used for taglines.
- Plan and check the travel path to avoid personnel and obstructions.
- Lift the load only high enough to clear the tallest obstruction in the travel path.
- Start and stop slowly.
- Land the load when the move is finished. Choose a safe landing.
- Never leave suspended loads unattended. In an emergency where the crane or hoist has become inoperative, if a load must be left suspended, barricade and post signs in the surrounding area, under the load, and on all four sides. Lock open and tag the crane or hoist main electrical disconnect switch.
PARKING A CRANE OR HOIST
- Remove all slings and accessories from the hook. Return the rigging device to the designated storage areas.
- Raise the hook at least 7 feet above the floor.
- Store the pendant away from aisles and work areas.
- Place the emergency stop switch (or push button) in the OFF position.
SLINGS & RIGGING
- PERFORMANCE CHARACTERISTICS OF NYLON Nylon is a popular and general purpose synthetic fiber which is unaffected by common grease and oil. Nylon slings are not suitable for use with acids and bleaching agents. Exposure can result in degradation from none to total. Dilute acids, such as hydrochloric and sulfuric in 10% concentration at room temperature cause a significant loss in strength in just 10 hours.
- Nylon products lose 15% of their workload when wet. The acceptable temperature exposure range is -40°F to a maximum of 194°F. Stretch at work load limit is approximately 6 – 8%. All nylon webbing will shrink overtime as a result of the weave configuration.
- SLING-TO-LOAD ANGLE - Slings with adequate workload limits to handle the “scale” weight of the load have catastrophically failed because of an inadequate consideration of the sling angle and the increased tension. Any load rigged in a hitch that is not vertical, develops increased tension on the sling. When selecting a sling, always consider the sling-to-load angle (horizontal angle) and the tension that will be applied to the sling.
- SLING-TO-LOAD ANGLE
Angle “A” Degrees |
Loss Factor |
Angle “A” Degrees |
Loss Factor |
90 |
1.000 |
55 |
.8192 |
85 |
.9962 |
50 |
.7660 |
80 |
.9848 |
45 |
.7071 |
75 |
.9659 |
40 |
.6428 |
70 |
.9397 |
35 |
.5736 |
65 |
.9063 |
30 |
.5000 |
60 |
.8660 |
25 |
.4226 |
Sling angles of less than 45° should not be used, unless approved by a qualified person
ENVIRONMENTAL CONSIDERATIONS
- WATER - When nylon products are wet they experience a 15% reduction in strength.
- ULTRAVIOLET (UV) LIGHT:
- Can affect the strength of synthetic webbing slings in varying degrees ranging from slight to total degradation
- Factors which affect the degree of strength loss are the length of continuous exposure time, sling construction, design and other environmental factors such as weather conditions, elevation and geographical location. Loss of strength for nylon slings can be 40 to 60% after exposure for periods ranging from 12 to 36 months.
- Visual indicators of UV degradation are a bleaching out of the sling color, increased stiffness of the sling material and the appearance of abrasion in areas not normally in contact with the load.
- Slings that are subject to continuous exposure to UV light should be proof tested to two times the work load limit, semi-annually, or more frequently depending on the severity of exposure.
- TEMPERATURE - Should never be used at temperatures in excess of 194°F. Cold temperature exposure to -40°F does not affect the strength of the synthetic sling.
- STORAGE:
- Store slings in a cool, dry, dark location, free of mechanical and environmental damage.
- The storage location should be ventilated and not exposed to heat sources, weld splatter, dust or grit and splinters from grinding.
- FOREIGN MATERIAL - Metal chips, weld spatter or heavy grit can damage a sling both externally and internally.
- CHEMICAL
- Chemically active environments – including those with a combustible dust that can be corrosive - can affect the strength of synthetic products in varying degrees ranging from moderate to total degradation.
- Before slings are used the chemical compatibility between the sling components and the environment must be considered – consult the sling manufacturer.
- OTHER POINTS TO REMEMBER
- Power or pressure washing can force residue inside the web fibers. The foreign material can cause internal yarn and fiber damage.
- Aluminum hardware is severely degraded by alkali, caustic and acidic environments. Aluminum hardware should never be exposed to chlorine environments or cleaned with chlorine based solutions. Steel hardware is not impervious to these elements – chemical and environmental compatibility must be assessed and suitability determined by the user.
SLING INSPECTIONS – THREE TYPES
- INITIAL
- This inspection is done when the sling is brand new - before the sling is used
- The inspection is done by an authorized person to ensure the sling is in the expected condition and to ensure that the correct sling is being used for the load
- Per the American Society of Mechanical Engineers “prior to use, all new, altered, modified or repaired slings shall be inspected by a designated person to verify compliance to all applicable standards.”
- FREQUENT
- This inspection should be done by the person handling the sling, before every use.
- The sling should be thoroughly examined and immediately removed from service if any damage is detected. Per OSHA, “each day before being used, the sling and all fastenings and attachments shall be inspected for damage and defects by a competent person designated by the employer.”
- PERIODIC
- This inspection is done at regular intervals and may be performed by a third party. The interval is based on the frequency of use, severity of the service conditions and information derived through the inspection process.
- Periodic inspection intervals shall not exceed one year intervals.
- ASME stated that guidelines for the inspection time intervals are as follows:
- Normal Service – Yearly
- Severe Service – Monthly or Quarterly
- Special Service – As recommended by a qualified person
REMOVAL FROM SERVICE CRITERIAL - Per OSHA 1910.184 – Synthetic slings shall be immediately removed from service if any of the following conditions are present:
- Acid or caustic burns
- Melting or charring on any art of the sling surface
- Snags, punctures, tears or cuts
- Broken or worn stitches
- Distortion of fittings
ASME B30.9 – Adds the following to the list from OSHA:
- Missing or illegible sling identification - must have
- name or trademark of manufacturer
- code number or stock number
- rated loads for the type of hitch used and the angle upon which it Is based
- The type of synthetic material
- Holes, tears, cuts or snags
- Broken or worn stitching in the load bearing splices
- Excessive abrasive wear
- Knots in any part of the sling
- Discoloration and brittle or stiff areas on any part of the sling
- Fittings that are pitted, corroded, cracked, bent, twisted, gouged or broken
“MINOR DAMAGE” - A brand new 3” wide nylon sling is expected to have a vertical load limit of 4800 lbs. with a 24,000 lb. (or higher) breaking strength. Now let’s look at what happens to the breaking strength of the sling when “minor damage” occurs:
- If the sling would receive a 1/8” cut the breaking strength drops to approximately 22,150 lbs.
- With a 1/4” cut the breaking of the sling drops to approximately 18,000 lbs.
- And with a cut of 3/8” the breaking strength of the sling drops to approximately 15,500 lbs. (that’s a loss of 35% of its breaking strength)
INSPECTING SLINGS - An inspection needs to be done before each use and only takes a few minutes if done properly.
- When inspecting the sling, twist and bend the sling in all directions – small cuts and abrasions can be almost invisible.
- When bending back the sling you may notice colored warning threads (most likely red in color) if you see red the sling must be taken out of service and replaced.
- These are a good indication that the sling has been damaged and the lifting capability compromised.
- Don’t rely on the warning threads because a sling can be compromised without the threads showing.
- If the warning threads are visible, frayed, or broken take the sling out of service immediately.
- Using your hands, start at one end of the sling and bend and twist the sling. Use your hands to feel any imperfections in the sling and look closely at the sling to see if anything unusual shows up.
- Check for any parts of the sling that has been elongated – especially the end loops (eyes) of the sling. A sling with elongated eyes has probably been used for a long time or has not been used properly or has been overloaded.
- If there is any part of a sling that is discolored, rough and stiff feeling or you can’t bend it over or twist it, that sling should be taken out of service immediately.
- Look for abrasions or scuffs, burns, cuts, unraveling, snags, punctures, broken stitching, UV degradation, embedded materials, melting, charring or knots – all of which can greatly reduce the slings load limit, and take the sling out of service immediately.
- When a sling is taken out of service it should be destroyed. St. Norbert College employees are not trained or authorized to repair a sling for reuse.
- When new slings are received, they should be inspected and cataloged and given a number designation in order to track the inspections and condition of the slings. The number designation should be written on the attached label or tag – not on the sling itself.
GENERAL RIGGING SAFETY REQUIREMENTS
Only select rigging equipment that is in good condition. All rigging equipment shall be inspected and recorded monthly; defective equipment is to be removed from service and destroyed to prevent inadvertent reuse. The load capacity limits shall be stamped or affixed to all rigging components. If there is no load capacity to be found on straps or wire rope then it’s not to be used and must be taken out of service.
An inspection checklist is provided so we are able to check rigging equipment monthly. St. Norbert College policy requires slings be rejected or destroyed if they do not meet the criteria noted on the checklist.
RIGGING A LOAD
Do the following when rigging a load:
- Determine the weight of the load. Do not guess.
- Determine the proper size for slings and components.
- Make sure that shackle pins and shouldered eye bolts are installed in accordance with the manufacturer’s recommendations.
- Make sure that ordinary eye bolts are threaded in at least 1.5 times the bolt diameter.
- Use safety hoist rings (swivel eyes) as a preferred substitute for eye bolts wherever possible.
- Pad sharp edges to protect slings. Remember that machinery foundations or angle-iron edges may not feel sharp to the touch but could cut into rigging when under several tons of load. Wood, tire rubber, or other pliable materials may be suitable for padding.
- Do not use slings, eye bolts, shackles, or hooks that have been cut, welded, or brazed.
- Install wire-rope clips with the base only on the live end and the U-bolt only on the dead end. Follow the manufacturer’s recommendations for the spacing for each specific wire size.
- Determine the center of gravity and balance the load before moving it.
- Initially lift the load only a few inches to test the rigging and balance.
SLING HITCHES
Slings carry their loads in one of three primary hitches and depending upon which hitch is used, it can affect the primary load limit of the sling. Most slings can be used for any of the three hitches but there are some slings that can only be used for a certain type of hitch. It is important to check the manufacturer’s recommendations to ensure you are using the proper sling for the desired hitch.
Slings have the largest work load limit when used in a basket hitch. The work load limit of a vertical hitch is 50% of the basket hitch. The same sling would be assigned a different work load limit for the choker hitch with a work load limit that is a maximum of 80% of the vertical work load limit (per ASME recommendation).
MECHANICAL AND OPERATIONAL CONSIDERATIONS
- Remember that work load limits and break strengths that are published by the manufacturer apply to only new and unused slings, assemblies and hardware. The numbers can go down depending upon the use and condition of the sling.
- Working load limits are also based on a moderately dynamic lifting or pulling operation. Instantaneous changes (drops or sudden pick ups) in excess of 10% of the workload constitute hazardous shock loading and the working load limits as stated, do not apply.
- Do not accelerate or decelerate the load too fast. The “G” force on a 1000 lbs. load dropped 3 feet could surpass the ultimate strength of the sling. A load picked up too fast can develop a stretch/friction/surface heat that will surpass the melting temperature of the sling.
- Wide body cargo and attached eye cargo slings are for use in Basket Hitches only. Hose handling, pipe lifting slings with quick disconnect and remote release slings are for use in Choker Hitches only.
WEAR PROTECTION - Synthetic slings can be damaged, abraded or cut as tension and compression between the sling, the connection points and the load develops. The edge of the load need not be “razor” sharp to damage the sling. Below are some tips for protection the slings from wear either from the load or from the environment:
- Load edges in contact with the sling must be “padded” with materials of sufficient thickness or strength to prevent sling damage. The protection must be installed and evaluated for suitability by raising the load slightly and then lowering the load for an inspection of the sling and the protection devices.
- Wear protection may not prevent cutting or other forms of sling damage. Keep personnel away from the load and they should never be under the load.
- Slings shall not be dragged on the ground, floor or over abrasive surfaces. Slings shall not be pulled from under loads when the load is resting on the sling. If possible place blocks on the ground and lower the load onto the blocks – this will allow for easy sling removal and no potential damage. Do not run over slings with trucks or other equipment.
CRANE OVERLOADING - Cranes or hoists shall not be loaded beyond their rated capacity for normal operations. Any crane or hoist suspected of having been overloaded shall be removed from service by locking open and tagging the main disconnect switch. Additionally, overloaded cranes shall be inspected, repaired, load tested, and approved by a professional before being returned to service.
- WORKING AT HEIGHTS ON CRANES OR HOISTS
- Any conducting maintenance or repair on cranes or hoists at heights greater than 6 feet shall use fall protection. Fall protection should also be considered for heights less than 6 feet. Fall protection includes safety harnesses that are fitted with a lifeline and securely attached to a structural member of the crane or building.
- Use of crane as work platform should only be considered when conventional means of reaching an elevated worksite are hazardous or not possible. Workers shall not ride a moving bridge crane.
- HAND SIGNALS - Signals to the operator shall be in accordance with the standard hand signals unless voice communications equipment (telephone, radio, or equivalent) is used signals shall be visible or audible at all times. Some special operations may require addition to or modification of the basic signals. For all such cases, these special signals shall be agreed upon and thoroughly understood by both the person giving the signals and the operator, and shall not be in conflict with the standard signals.
- INSPECTION, MAINTENANCE, AND TESTING - All tests and inspections shall be conducted in accordance with the manufacturer’s recommendations.
- ANNUAL INSPECTIONS - The manager will schedule an annual preventive maintenance (PM) and/or annual inspections of all cranes and hoists own by St. Norbert College. The annual PM and inspection must be done by a professional and all documentation must be kept on record. A copy should be retained by the department and a copy.
- LOAD TESTING - If a crane has known to be overloaded of its capacity or has had any modifications done to it, it will have to be load tested. If load testing is necessary it will only be done by a professional. A copy should be retained by the department.
RECORDS
Managers are responsible to maintain all records for St. Norbert College owned cranes, hoist, slings, and other rigging equipment.
PROGRAM REVIEW AND UPDATE - This policy shall be reviewed and updated on an annual basis or sooner if necessary.
Contact Us
Location
Our office is located on First Street in the Garden Level (lower level) of Main Hall in De Pere, Wis.
Campus Map
Hours of Operation
Monday-Friday
8 a.m.-4:30 p.m.
Phone: 920-403-3211
Fax: 920-403-3983
Email: hr@snc.edu