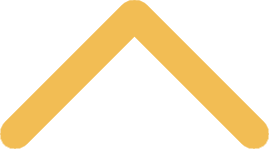
Safety: Fall Protection
Applies to: All faculty, staff, and any contractors working on St. Norbert College property
Purpose: To ensure all areas are free from uncontrolled fall hazards, all employees are properly trained in fall prevention and protection, and fall prevention systems are inspected and monitored to ensure effectiveness. This policy will follow the OSHA standard for potential falls from heights of 4 feet (general industry) or 6 feet (construction). First consideration should be given to the elimination of fall hazards. If a fall hazard cannot be eliminated, effective fall protection will be planned, implemented, and monitored to control the risks of injury due to falling. All employees exposed to potential falls from heights will be trained to minimize the exposures. Fall protection equipment will be provided and its use required by all employees.
Policy Owner: Human Resources
Revision Dates: February 2018, June 2018, December 2022
Policy
RESPONSIBILITIES
Departments - Each department is responsible for compliance with the criteria set forth in this policy. They must insure that all elements of this policy and related procedures are implemented and followed.
Sr. Benefits and Safety Specialist
- Review changes in operations and keep current with new processes and/or facilities within the College and identify new Fall Protection requirements when needed.
- Work with managers and coordinate efforts to analyze, minimize occupational exposures.
- Document and maintain training records.
Departmental Managers
- Implement and enforce fall protection requirements within their respective area(s) of responsibility to ensure compliance with all aspects of this policy.
- Provide personal protective equipment (PPE) to all applicable employees and communicate the necessary PPE requirements.
- Evaluate the workplace to identify substandard or otherwise hazardous conditions, which may require administrative controls, engineering controls, PPE, or any combination thereof as a means to ensure employee health and safety as it concerns fall protection.
- Ensure that employees who are working aloft or are at risk for falls receive periodic training including the proper use and limitations of their PPE.
- Ensure that all employees understand the job tasks or areas which that make them subject to this policy.
- Promote employee feedback as it pertains to fall protection.
- Establish and maintain a system, which assures the proper cleaning, maintenance and storage of all PPE pertaining to fall protection.
Employees
- Use PPE as instructed and in accordance with training received for fall protection.
- Maintain PPE and report any damage or loss to supervisor or manager.
Procedures
FALL HAZARD IDENTIFICATION / EVALUATION - On a jobsite, the supervisor or lead worker (as designated by the Director of Facilities or their designee) will be responsible for identifying fall hazards. The site supervisor will evaluate each situation or work procedure where employees may be exposed to a fall of 6 feet or more. The supervisor or lead worker (as designated by the Director of Facilities or their designee) will be responsible for developing a plan to eliminate the exposures, if possible, or to select the appropriate fall protection systems and/or equipment.
- Wall Openings – Each employee working on, at, above, or near wall openings (including those with chutes attached) where the outside bottom edge of the wall opening is 6 feet or more above lower levels and the inside bottom edge of the wall opening is less than 39 inches above the walking/working surface must be protected from falling by the use of a guardrail system, a safety net system, or a personal fall arrest system.
- Holes – Personal fall arrest systems, covers, or guardrail systems shall be erected around holes (including skylights) that are more than 6 feet above lower levels.
- Leading Edges – Each employee who is constructing a leading edge, 6 feet or more above lower levels, shall be protected by guardrail systems, safety net systems, or personal fall arrest systems.
- Formwork and Reinforcing Steel – For employees, while moving vertically and/or horizontally on the vertical face of rebar assemblies built in place, fall protection is not required when employees are moving. OSHA considers the multiple hand holds and foot holds on rebar assemblies as providing similar protection as that provided by a fixed ladder, consequently, no fall protection necessary while moving point to point for heights below 20 feet. An employee must be provided with fall protection or prevention measures when climbing or otherwise moving at a height more than 20 feet, the same as for fixed ladders.
- Hoist Areas – Each employee in a hoist area shall be protected from falling 6 feet or more by guardrail systems or personal fall arrest systems. If guardrail systems or portions thereof must be removed to facilitate hoisting operations, as during the landing of materials, and a worker must lean through the access opening or out over the edge of the access opening to receive or guide equipment or materials, that employee must be protected by a personal fall arrest system.
- Ramps, Runways, and Other Walkways – Each employee using ramps, runways, and other walkways shall be protected from falling 6 feet or more by guardrail systems.
- Low-Slope Roofs – Each employee engaged in roofing activities on low-slope roofs with unprotected sides and edges 6 feet or move above lower levels shall be protected from falling by guardrail system, safety net systems, personal fall arrest systems or a combination of a warning line system and guardrail system, warning line system and safety net system, warning line system and personal fall arrest system, or warning line system and safety monitoring system. On roofs 50 feet or less in width, the use of a safety monitoring system without a warning line system is permitted.
- Steep Roofs – Each employee on a steep roof with unprotected sides and edges 6 feet or more above lower levels shall be protected by guardrail systems with toe boards, safety net systems, or personal fall arrest systems.
- Controlled Access Zones – A controlled access zone is a work area designated and clearly marked in which certain types of work may take place without the use of conventional fall protection systems – guardrail, personal arrest or safety net – to protect the employees working in the zone.
- Controlled access zones are used to keep out workers other than those authorized to enter work areas from which guardrails have been removed.
- Controlled access zones, when created to limit entrance to areas where leading edge work and other operations are taking place, must be defined by a control line or by any other means that restrict access. Control lines shall consist of ropes, wires, tapes or equivalent materials, and supporting stanchions, and each must be:
- Flagged or otherwise clearly marked at not more than 6 foot intervals with high-visibility material.
- Rigged and supported in such a way that the lowest point (including sag) is not less than 39 inches from the walking/working surface and the highest point is not more that 45 inches – nor more than 50 inches when overhand bricklaying operations are being performed – from the walking/working surface.
- Strong enough to sustain stress of not less than 200 pounds. Control lines shall extend along the entire length of the unprotected or leading edge and shall be approximately parallel to the unprotected or leading edge.
- Control lines also must be connected on each side to a guardrail system or wall.
- When control lines are used, they shall be erected not less than 6 feet nor more than 25 feet from the unprotected or leading edge, except when precast concrete members are being erected. In the latter case, the control line is to be erected not less than 6 feet nor more than 60 feet or half the length of the member being erected, whichever is less, from the leading edge.
- Controlled access zones when used to determine access to areas where overhand bricklaying and related work are taking place are to be defined by a control line erected not less than 10 feet not more than 15 feet from the working edge. Additional control lines must be erected at each end to enclose the controlled access zone. Only employees engaged in overhand bricklaying or related work, are permitted in the controlled access zones.
- On floors and roofs where guardrail systems are not in place prior to the beginning of overhand bricklaying operations, controlled access zones will be enlarged as necessary to enclose all points of access, material handling areas, and storage areas.
- On floors and roofs where guardrail systems are in place, but need to be removed to allow overhand bricklaying work or leading edge work to take place, only that portion of the guardrail necessary to accomplish that day’s work shall be removed.
FALL PROTECTION SYSTEMS - When there is a potential fall of 6 feet or more, we will utilize one or more of the following means of providing protection:
- Guardrail Systems
- Guardrail systems must meet the following criteria. Top rails and midrails of guardrail systems must be at least one-quarter inch nominal diameter or thickness to prevent cuts and lacerations. If wire rope is used for top rails, it must be flagged at not more than 6 foot intervals with high-visibility material. Steel and plastic banding cannot be used as top rails or midrails. Manila, plastic, or synthetic rope used for top rails or midrails must be inspected as frequently as necessary to ensure strength and stability.
- The top edge height of top rails, or guardrails must be 42 inches plus or minus 3 inches, above the walking/working level. When workers are using stilts, the top edge height of the top rail, or equivalent member, must be increased an amount equal to the height of the stilts.
- Screens, midrails, mesh, intermediate vertical members, or equivalent intermediate structural members must be installed between the top edge of the guardrail system and the walking/working surface when there are no walls or parapet walls at least 21 inches high. When midrails are used, they must be installed at a height midway between the top edge of the guardrail system and the walking/working level. When screens and mesh are used, they must extend from the top rail to the walking/working level and along the entire opening between top rail supports. Intermediate members, such as balusters, when used between posts, shall not be more than 19 inches apart.
- Other structural members, such as additional midrails and architectural panels, shall be installed so that there are no openings in the guardrail system more than 19 inches.
- The guardrail system must be capable of withstanding a force of at least 200 pounds applied within 2 inches of the top edge in any outward or downward direction. When the 200-pound test is applied in a downward direction, the top edge of the guardrail must not deflect to a height less than 39 inches above the walking/working level.
- Midrails, screens, mesh, intermediate vertical members, solid panels, and equivalent structural members shall be capable of withstanding a force of at least 150 pounds applied in any downward or outward direction at any point along the midrail or other member.
- Guardrail systems shall be surfaced to protect workers from punctures or lacerations and to prevent clothing from snagging.
- The ends of top rails and midrails must not overhang terminal posts, except where such overhang does not constitute a projection hazard.
- When guardrail systems are used at hoisting areas, a chain, gate or removable guardrail section must be placed across the access opening between guardrail sections when hoisting operations are not taking place.
- At holes, guardrail systems must be set up on all unprotected sides or edges. When holes are used for the passage of materials, the hole shall have not more than two sides with removable guardrail sections. When the hole is not in use, it must be covered or provided with guardrails along all unprotected sides or edges.
- If guardrail systems are used around holes that are used as access points (such as ladder ways), gates must be used or the point of access must be offset to prevent accidental walking into the hole.
- If guardrails are used at unprotected sides or edges of ramps and runways, they must be erected on each unprotected side or edge.
- Personal Fall Arrest Systems - These consist of an anchorage, connectors, and a body harness and may include a deceleration device, lifeline, or suitable combinations. If a personal fall arrest system is used for fall protection, it must do the following:
- Limit maximum arresting force on an employee to 1,800 pounds when used with a body harness.
- Be rigged so that an employee can neither free fall more than 6 feet nor contact any lower level.
- Bring an employee to a complete stop and limit maximum deceleration distance an employee travels to 3.5 feet.
- Have sufficient strength to withstand twice the potential impact energy on an employee free falling a distance of 6 feet or the free fall distance permitted by the system, whichever is less.
- The use of body belts for fall arrest is prohibited and a full body harness is required.
- Personal fall arrest systems must be inspected prior to each use for wear damage, and other deterioration. Defective components must be removed from service.
- Positioning Device Systems - These body harness systems are to be set up so that a worker can free fall no farther than 2 feet. They shall be secured to an anchorage capable of supporting at least twice the potential impact load of an employee’s fall or 5,000 pounds, whichever is greater.
- Safety Monitoring Systems - Whenever no alternative fall protection has been implemented, the employer shall implement a safety monitoring system. Employers must appoint a competent person to monitor the safety of workers and the employer shall ensure that the safety monitor:
- Is competent in the recognition of fall hazards.
- Is capable of warning workers of fall hazard dangers and in detecting unsafe work practices.
- Is operating on the same walking/working surfaces of the workers and can see them.
- Is close enough to work operation to communicate orally with workers and has no other duties to distract from the monitoring function.
- Mechanical equipment shall not be used or stored in areas where safety-monitoring systems are being used to monitor employees engaged in roofing operation on low-sloped roofs.
- No worker, other than the one engaged in roofing work (on low-sloped roofs) or the one covered by a fall protection plan, shall be allowed in an area where an employee is being protected by a safety monitoring system.
- All workers in a controlled access zone shall be instructed to promptly comply with fall hazard warnings issued by safety monitors.
- Safety Net Systems
- Safety nets must be installed as close as practicable under the walking/working surface on which employees are working and never more than 30 feet below such levels. Defective nets shall not be used. Safety nets shall be inspected at least once a week for wear, damage, and other deterioration. Safety nets shall be installed with sufficient clearance underneath to prevent contact with the surface or structure below.
- Items that have fallen into safety nets including – but not restricted to, materials, scrap, equipment, and tools – must be removed as soon as possible and at least before the next work shift.
- Warning Line Systems - Warning line systems consist of ropes, wires, or chains, and supporting stanchions and are set up as follows:
- Flagged at not more than 6-foot intervals with high-visibility material.
- Rigged and supported so that the lowest point (including sag) is no less than 34 inches from the walking/working surface and its highest point is no more than 39 inches from the walking/working surface.
- Stanchions, after being rigged with warning lines, shall be capable of resisting, without tipping over, a force of at least 16 pounds applied horizontally against the stanchion, 30 inches above the walking/working surface, perpendicular to the warning line and in the direction of the floor, roof, or platform edge.
- The rope, wire, or chain shall have a minimum tensile strength of 500 pounds and after being attached to the stanchions, must support without breaking the load applied to the stanchions as prescribed above.
- Shall be attached to each stanchion is such a way that pulling on one section of the line between stanchions will not result in slack being taken up in the adjacent section before the stanchion tips over.
- Warning lines shall be erected around all sides of roof work areas. When mechanical equipment is being used, the warning line shall be erected not less than 6 feet from the roof edge parallel to the direction of mechanical equipment operation, and not less than 10 feet from the roof edge perpendicular to the direction of mechanical equipment operation.
- When mechanical equipment is not being used, the warning line must be erected not less than 6 feet from the roof edge.
- Covers - Covers located in roadways and vehicle aisles must be able to support at least twice the maximum axle load of the largest vehicle to which the cover might be subjected. All other covers must be able to support at least twice the weight of employees, equipment, and materials that may be imposed on the cover at any one time. To prevent accidental displacement resulting from wind, equipment or workers activities, all covers must be secured. All covers shall be color-coded or bear the markings “HOLE” or “COVER”.
- Protection from Falling Objects
- When guardrail systems are used to prevent materials from falling from one level to another, any openings must be small enough to prevent passage of potential falling objects. No materials or equipment except masonry and mortar shall be stored within 4 feet or working edges. Excess mortar, broken or scattered masonry units, and all other materials and debris shall be kept clear of the working area by removal at regular intervals.
- During roofing work, materials and equipment shall not be stored within 6 feet of a roof edge unless guardrails are erected at the edge, and materials piled, grouped, or stacked near a roof edge must be stable and self-supporting.
TRAINING - Employees will be trained in the following areas:
- The nature of fall hazards in the work area.
- The correct procedures for erecting, maintaining, disassembling, and inspecting fall protection systems.
- The use and operation of controlled access zones and guardrail, personal fall arrest, safety net, warning line, and safety monitoring systems.
- The role of each employee in the safety monitoring system when the system is in use.
- The limitations on the use of mechanical equipment during the performance of roofing work on low-sloped roofs.
- The correct procedures for equipment and materials handling and storage and the erection of overhead protection.
- Employees’ role in fall protection plans.
- The correct use, inspection and maintenance of fall protection (harnesses, lanyards, etc.) and fall prevention systems.
- Re-training in fall protection is performed as necessary.
- Training is documented and uploaded to the training folder.
- All incidents involving a fall from elevation will be investigated and followed up on to ensure that it does not happen again.
RESCUE
- Purpose - The purpose of this rescue plan is to establish College wide guidelines for responding to falls from height. This rescue plan is intended to reduce risks to an employee’s health after a fall arrest event. The rescue plan should also minimize the amount of at-risk behavior of the rescuer during the rescue attempt, and help to ensure that the rescue is conducted promptly in a safe and professional manner.
- Application
- This rescue plan applies to all locations where personnel are employed to work at height.
- The requirements of this rescue plan must be observed by all personnel involved in working at heights.
- This rescue plan must be reviewed or included in any job safety analysis or pre-task planning for activities that require working at heights.
- Definitions
- Rescue Plan: A strategy or procedure, planned in advance, to safely retrieve a person who has fallen from an elevated work surface and is suspended in a full body harness. This includes self-rescue or mechanically aided rescue.
- Self Rescue: An act or instance of an employee using his fall protection equipment to rescue him or herself.
- Mechanically Aided Rescue: A strategy or procedure, planned in advance, to safely retrieve a person who has fallen from an elevated work surface using mechanical means.
- Suspension Trauma: A serious medical condition that can lead to unconsciousness, injury or death, which can occur when a worker is suspended in a harness for too long after a fall.
- Prompt Rescue: The recommended goal for rescue subject contact is less than six minutes, per ANSI Z359.2-6.1.
- Rescue Responsibilities
- Employees:
- Must be trained in and familiar with the Fall Protection Policy.
- Must understand and be able to evaluate the risks associated with working at heights.
- Must be trained and competent in the use of fall protection equipment prior to conducting work at heights.
- Must report unsafe conditions or behaviors to the supervisor or lead worker (as designated by the Director of Facilities or their designee).
- Must be familiar with and understand the College’s rescue plan to provide prompt rescue in the event of an arrested fall event.
- Employees:
- Authorized Rescuer: Must be trained by a competent rescuer trainer before being exposed to a fall hazard or potential rescue application.
- Must be re-trained when the nature of the work, workplace, or methods of control or rescue change to an extent that prior training is no longer adequate.
- Must be trained on how to inspect, anchor, assemble and use the fall protection and rescue equipment used in locations where employees work. Training must include physical demonstrations by trainees.
- Training must include at least the following:
- Fall hazard recognition;
- Fall hazard elimination and control methods;
- Applicable fall protection and rescue regulations;
- How to use written fall protection and rescue procedures;
- Inspection of equipment components and systems before use.
-
- Refresher training must occur at least every two years for the authorized rescuer to stay current with fall protection and rescue educational requirements per ANSI.
- Must be evaluated by a competent rescuer or competent rescuer trainer at least annually to ensure competency of the duties assigned. This evaluation must include both a written examination and a physical demonstration of usage of all equipment the person is authorized to operate.
- Competent Rescuer:
- Must be trained by a competent rescuer trainer.
- Must be trained on how to inspect, anchor, assemble and use the fall protection and rescue equipment used in locations where employees work. Training must include physical demonstrations by trainees.
- Training must include use of all types of equipment and systems used in locations where rescues may be required, including inspection of systems prior to use, installation, component compatibility, descent control, secondary systems, packaging methods, dismantling, storage and the common hazards associated with each system and component.
- Training must include at least the following information:
- Fall hazard elimination and control methods;
- Applicable fall protection and rescue regulations;
- Assessment of fall hazards to determine rescue methods;
- Responsibilities of designated persons under this standard;
- Detailed inspection and recording of rescue equipment components and systems;
- Rescue systems assessment and determination of when a system is unsafe;
- Development of written fall protection rescue procedures;
- Selection and use of non-certified anchorages.
- Refresher training for Competent Person Rescuers must be conducted at least every year per ANSI.
- Rescue Procedure - A rescue plan must be identified for any job that requires work at height. The rescue plan must include consideration of the following rescue types and circumstances:
- Self Rescue - If the person working at heights has properly selected and used his or her fall protection equipment, 90% of workers will be able to perform a Self Rescue, which should include these steps:
- Climbing back up to the level from which he fell (from a few inches to 2-3 feet).
- Returning to the floor or ground to be evaluated for possible medical attention per OSHA.
- Removing all components of fall arrest system impacted by the fall event from service and documenting (bag and tag) the components with name, date and activity at time of fall and giving the equipment to management.
- Assisted Self Rescue with Mechanically Aided Hauling/Rope System - If self-rescue is not possible, then an Assisted Self Rescue will be needed. The following guidelines should be used during a mechanically aided rescue:
- A compliant rescue and descent device will be secured to an anchor that is rated for at least 3,000 lbs.
- The haul line may be swung over or lowered to the fallen worker, who will grab the rescue lifeline snap hook and secure it to the appropriate D-ring on his body support. A positive connection to the D-ring must be verified by one of the rescue team members.
- The rescue team will raise or lower the fallen employee to the appropriate work platform or ground and provide medical aid as required by OSHA.
- Remove all components of fall arrest system impacted by the fall event from service and document (bag and tag) the components with name, date and activity at time of fall and give the equipment to management.
- Mechanically Aided (unconscious) with hauling/rope system - If the worker’s injuries prevent the worker from attaching to the rescue system, both self-rescue and assisted self-rescue are not options, and a fully Assisted Rescue is necessary:
- A compliant rescue and descent device will be secured to an anchor that is rated for at least 3,000 lbs.
- A rescue team member must attach the haul line to the worker’s fall arrest system. This can be performed by accessing the fallen worker and then attaching the rescue system directly to a D-ring on the worker’s harness, or by using a rescue pole for the attachment. The rescue team could also attach a rescue grab to the lanyard or vertical lifeline.
- The rescue team must raise or lower the fallen worker to the appropriate work platform or ground and provide medical aid as required by OSHA.
- Remove all components of fall arrest system impacted by the fall event from service and document (bag and tag) the components with name, date and activity at time of fall and give the equipment to management.
- Assisted rescue with mechanically aided aerial lift - If another means of performing a fully Assisted Rescue is to use an aerial lift under the following guidelines:
- A rescuer will get into the aerial lift and make sure there is a second fall protection device, such as a shock absorbing lanyard or self-retracting lifeline available for the fallen worker.
- The aerial lift must be maneuvered into position (raised up underneath the fallen worker) so that the rescuer can perform the rescue.
- Attach the second lanyard or self-retracting lifeline in the aerial lift to the fallen worker.
- Disconnect the rescued worker from the impacted fall arrest equipment.
- Lower the worker to the ground and provide medical aid as required by OSHA.
- Remove all components of fall arrest system impacted by the fall event from service and document (bag and tag) the components with name, date and activity at time of fall and give the equipment to management
- Self Rescue - If the person working at heights has properly selected and used his or her fall protection equipment, 90% of workers will be able to perform a Self Rescue, which should include these steps:
Policy
RESPONSIBILITIES
Departments - Each department is responsible for compliance with the criteria set forth in this policy. They must insure that all elements of this policy and related procedures are implemented and followed.
Sr. Benefits and Safety Specialist
- Review changes in operations and keep current with new processes and/or facilities within the College and identify new Fall Protection requirements when needed.
- Work with managers and coordinate efforts to analyze, minimize occupational exposures.
- Document and maintain training records.
Departmental Managers
- Implement and enforce fall protection requirements within their respective area(s) of responsibility to ensure compliance with all aspects of this policy.
- Provide personal protective equipment (PPE) to all applicable employees and communicate the necessary PPE requirements.
- Evaluate the workplace to identify substandard or otherwise hazardous conditions, which may require administrative controls, engineering controls, PPE, or any combination thereof as a means to ensure employee health and safety as it concerns fall protection.
- Ensure that employees who are working aloft or are at risk for falls receive periodic training including the proper use and limitations of their PPE.
- Ensure that all employees understand the job tasks or areas which that make them subject to this policy.
- Promote employee feedback as it pertains to fall protection.
- Establish and maintain a system, which assures the proper cleaning, maintenance and storage of all PPE pertaining to fall protection.
Employees
- Use PPE as instructed and in accordance with training received for fall protection.
- Maintain PPE and report any damage or loss to supervisor or manager.
Procedures
FALL HAZARD IDENTIFICATION / EVALUATION - On a jobsite, the supervisor or lead worker (as designated by the Director of Facilities or their designee) will be responsible for identifying fall hazards. The site supervisor will evaluate each situation or work procedure where employees may be exposed to a fall of 6 feet or more. The supervisor or lead worker (as designated by the Director of Facilities or their designee) will be responsible for developing a plan to eliminate the exposures, if possible, or to select the appropriate fall protection systems and/or equipment.
- Wall Openings – Each employee working on, at, above, or near wall openings (including those with chutes attached) where the outside bottom edge of the wall opening is 6 feet or more above lower levels and the inside bottom edge of the wall opening is less than 39 inches above the walking/working surface must be protected from falling by the use of a guardrail system, a safety net system, or a personal fall arrest system.
- Holes – Personal fall arrest systems, covers, or guardrail systems shall be erected around holes (including skylights) that are more than 6 feet above lower levels.
- Leading Edges – Each employee who is constructing a leading edge, 6 feet or more above lower levels, shall be protected by guardrail systems, safety net systems, or personal fall arrest systems.
- Formwork and Reinforcing Steel – For employees, while moving vertically and/or horizontally on the vertical face of rebar assemblies built in place, fall protection is not required when employees are moving. OSHA considers the multiple hand holds and foot holds on rebar assemblies as providing similar protection as that provided by a fixed ladder, consequently, no fall protection necessary while moving point to point for heights below 20 feet. An employee must be provided with fall protection or prevention measures when climbing or otherwise moving at a height more than 20 feet, the same as for fixed ladders.
- Hoist Areas – Each employee in a hoist area shall be protected from falling 6 feet or more by guardrail systems or personal fall arrest systems. If guardrail systems or portions thereof must be removed to facilitate hoisting operations, as during the landing of materials, and a worker must lean through the access opening or out over the edge of the access opening to receive or guide equipment or materials, that employee must be protected by a personal fall arrest system.
- Ramps, Runways, and Other Walkways – Each employee using ramps, runways, and other walkways shall be protected from falling 6 feet or more by guardrail systems.
- Low-Slope Roofs – Each employee engaged in roofing activities on low-slope roofs with unprotected sides and edges 6 feet or move above lower levels shall be protected from falling by guardrail system, safety net systems, personal fall arrest systems or a combination of a warning line system and guardrail system, warning line system and safety net system, warning line system and personal fall arrest system, or warning line system and safety monitoring system. On roofs 50 feet or less in width, the use of a safety monitoring system without a warning line system is permitted.
- Steep Roofs – Each employee on a steep roof with unprotected sides and edges 6 feet or more above lower levels shall be protected by guardrail systems with toe boards, safety net systems, or personal fall arrest systems.
- Controlled Access Zones – A controlled access zone is a work area designated and clearly marked in which certain types of work may take place without the use of conventional fall protection systems – guardrail, personal arrest or safety net – to protect the employees working in the zone.
- Controlled access zones are used to keep out workers other than those authorized to enter work areas from which guardrails have been removed.
- Controlled access zones, when created to limit entrance to areas where leading edge work and other operations are taking place, must be defined by a control line or by any other means that restrict access. Control lines shall consist of ropes, wires, tapes or equivalent materials, and supporting stanchions, and each must be:
- Flagged or otherwise clearly marked at not more than 6 foot intervals with high-visibility material.
- Rigged and supported in such a way that the lowest point (including sag) is not less than 39 inches from the walking/working surface and the highest point is not more that 45 inches – nor more than 50 inches when overhand bricklaying operations are being performed – from the walking/working surface.
- Strong enough to sustain stress of not less than 200 pounds. Control lines shall extend along the entire length of the unprotected or leading edge and shall be approximately parallel to the unprotected or leading edge.
- Control lines also must be connected on each side to a guardrail system or wall.
- When control lines are used, they shall be erected not less than 6 feet nor more than 25 feet from the unprotected or leading edge, except when precast concrete members are being erected. In the latter case, the control line is to be erected not less than 6 feet nor more than 60 feet or half the length of the member being erected, whichever is less, from the leading edge.
- Controlled access zones when used to determine access to areas where overhand bricklaying and related work are taking place are to be defined by a control line erected not less than 10 feet not more than 15 feet from the working edge. Additional control lines must be erected at each end to enclose the controlled access zone. Only employees engaged in overhand bricklaying or related work, are permitted in the controlled access zones.
- On floors and roofs where guardrail systems are not in place prior to the beginning of overhand bricklaying operations, controlled access zones will be enlarged as necessary to enclose all points of access, material handling areas, and storage areas.
- On floors and roofs where guardrail systems are in place, but need to be removed to allow overhand bricklaying work or leading edge work to take place, only that portion of the guardrail necessary to accomplish that day’s work shall be removed.
FALL PROTECTION SYSTEMS - When there is a potential fall of 6 feet or more, we will utilize one or more of the following means of providing protection:
- Guardrail Systems
- Guardrail systems must meet the following criteria. Top rails and midrails of guardrail systems must be at least one-quarter inch nominal diameter or thickness to prevent cuts and lacerations. If wire rope is used for top rails, it must be flagged at not more than 6 foot intervals with high-visibility material. Steel and plastic banding cannot be used as top rails or midrails. Manila, plastic, or synthetic rope used for top rails or midrails must be inspected as frequently as necessary to ensure strength and stability.
- The top edge height of top rails, or guardrails must be 42 inches plus or minus 3 inches, above the walking/working level. When workers are using stilts, the top edge height of the top rail, or equivalent member, must be increased an amount equal to the height of the stilts.
- Screens, midrails, mesh, intermediate vertical members, or equivalent intermediate structural members must be installed between the top edge of the guardrail system and the walking/working surface when there are no walls or parapet walls at least 21 inches high. When midrails are used, they must be installed at a height midway between the top edge of the guardrail system and the walking/working level. When screens and mesh are used, they must extend from the top rail to the walking/working level and along the entire opening between top rail supports. Intermediate members, such as balusters, when used between posts, shall not be more than 19 inches apart.
- Other structural members, such as additional midrails and architectural panels, shall be installed so that there are no openings in the guardrail system more than 19 inches.
- The guardrail system must be capable of withstanding a force of at least 200 pounds applied within 2 inches of the top edge in any outward or downward direction. When the 200-pound test is applied in a downward direction, the top edge of the guardrail must not deflect to a height less than 39 inches above the walking/working level.
- Midrails, screens, mesh, intermediate vertical members, solid panels, and equivalent structural members shall be capable of withstanding a force of at least 150 pounds applied in any downward or outward direction at any point along the midrail or other member.
- Guardrail systems shall be surfaced to protect workers from punctures or lacerations and to prevent clothing from snagging.
- The ends of top rails and midrails must not overhang terminal posts, except where such overhang does not constitute a projection hazard.
- When guardrail systems are used at hoisting areas, a chain, gate or removable guardrail section must be placed across the access opening between guardrail sections when hoisting operations are not taking place.
- At holes, guardrail systems must be set up on all unprotected sides or edges. When holes are used for the passage of materials, the hole shall have not more than two sides with removable guardrail sections. When the hole is not in use, it must be covered or provided with guardrails along all unprotected sides or edges.
- If guardrail systems are used around holes that are used as access points (such as ladder ways), gates must be used or the point of access must be offset to prevent accidental walking into the hole.
- If guardrails are used at unprotected sides or edges of ramps and runways, they must be erected on each unprotected side or edge.
- Personal Fall Arrest Systems - These consist of an anchorage, connectors, and a body harness and may include a deceleration device, lifeline, or suitable combinations. If a personal fall arrest system is used for fall protection, it must do the following:
- Limit maximum arresting force on an employee to 1,800 pounds when used with a body harness.
- Be rigged so that an employee can neither free fall more than 6 feet nor contact any lower level.
- Bring an employee to a complete stop and limit maximum deceleration distance an employee travels to 3.5 feet.
- Have sufficient strength to withstand twice the potential impact energy on an employee free falling a distance of 6 feet or the free fall distance permitted by the system, whichever is less.
- The use of body belts for fall arrest is prohibited and a full body harness is required.
- Personal fall arrest systems must be inspected prior to each use for wear damage, and other deterioration. Defective components must be removed from service.
- Positioning Device Systems - These body harness systems are to be set up so that a worker can free fall no farther than 2 feet. They shall be secured to an anchorage capable of supporting at least twice the potential impact load of an employee’s fall or 5,000 pounds, whichever is greater.
- Safety Monitoring Systems - Whenever no alternative fall protection has been implemented, the employer shall implement a safety monitoring system. Employers must appoint a competent person to monitor the safety of workers and the employer shall ensure that the safety monitor:
- Is competent in the recognition of fall hazards.
- Is capable of warning workers of fall hazard dangers and in detecting unsafe work practices.
- Is operating on the same walking/working surfaces of the workers and can see them.
- Is close enough to work operation to communicate orally with workers and has no other duties to distract from the monitoring function.
- Mechanical equipment shall not be used or stored in areas where safety-monitoring systems are being used to monitor employees engaged in roofing operation on low-sloped roofs.
- No worker, other than the one engaged in roofing work (on low-sloped roofs) or the one covered by a fall protection plan, shall be allowed in an area where an employee is being protected by a safety monitoring system.
- All workers in a controlled access zone shall be instructed to promptly comply with fall hazard warnings issued by safety monitors.
- Safety Net Systems
- Safety nets must be installed as close as practicable under the walking/working surface on which employees are working and never more than 30 feet below such levels. Defective nets shall not be used. Safety nets shall be inspected at least once a week for wear, damage, and other deterioration. Safety nets shall be installed with sufficient clearance underneath to prevent contact with the surface or structure below.
- Items that have fallen into safety nets including – but not restricted to, materials, scrap, equipment, and tools – must be removed as soon as possible and at least before the next work shift.
- Warning Line Systems - Warning line systems consist of ropes, wires, or chains, and supporting stanchions and are set up as follows:
- Flagged at not more than 6-foot intervals with high-visibility material.
- Rigged and supported so that the lowest point (including sag) is no less than 34 inches from the walking/working surface and its highest point is no more than 39 inches from the walking/working surface.
- Stanchions, after being rigged with warning lines, shall be capable of resisting, without tipping over, a force of at least 16 pounds applied horizontally against the stanchion, 30 inches above the walking/working surface, perpendicular to the warning line and in the direction of the floor, roof, or platform edge.
- The rope, wire, or chain shall have a minimum tensile strength of 500 pounds and after being attached to the stanchions, must support without breaking the load applied to the stanchions as prescribed above.
- Shall be attached to each stanchion is such a way that pulling on one section of the line between stanchions will not result in slack being taken up in the adjacent section before the stanchion tips over.
- Warning lines shall be erected around all sides of roof work areas. When mechanical equipment is being used, the warning line shall be erected not less than 6 feet from the roof edge parallel to the direction of mechanical equipment operation, and not less than 10 feet from the roof edge perpendicular to the direction of mechanical equipment operation.
- When mechanical equipment is not being used, the warning line must be erected not less than 6 feet from the roof edge.
- Covers - Covers located in roadways and vehicle aisles must be able to support at least twice the maximum axle load of the largest vehicle to which the cover might be subjected. All other covers must be able to support at least twice the weight of employees, equipment, and materials that may be imposed on the cover at any one time. To prevent accidental displacement resulting from wind, equipment or workers activities, all covers must be secured. All covers shall be color-coded or bear the markings “HOLE” or “COVER”.
- Protection from Falling Objects
- When guardrail systems are used to prevent materials from falling from one level to another, any openings must be small enough to prevent passage of potential falling objects. No materials or equipment except masonry and mortar shall be stored within 4 feet or working edges. Excess mortar, broken or scattered masonry units, and all other materials and debris shall be kept clear of the working area by removal at regular intervals.
- During roofing work, materials and equipment shall not be stored within 6 feet of a roof edge unless guardrails are erected at the edge, and materials piled, grouped, or stacked near a roof edge must be stable and self-supporting.
TRAINING - Employees will be trained in the following areas:
- The nature of fall hazards in the work area.
- The correct procedures for erecting, maintaining, disassembling, and inspecting fall protection systems.
- The use and operation of controlled access zones and guardrail, personal fall arrest, safety net, warning line, and safety monitoring systems.
- The role of each employee in the safety monitoring system when the system is in use.
- The limitations on the use of mechanical equipment during the performance of roofing work on low-sloped roofs.
- The correct procedures for equipment and materials handling and storage and the erection of overhead protection.
- Employees’ role in fall protection plans.
- The correct use, inspection and maintenance of fall protection (harnesses, lanyards, etc.) and fall prevention systems.
- Re-training in fall protection is performed as necessary.
- Training is documented and uploaded to the training folder.
- All incidents involving a fall from elevation will be investigated and followed up on to ensure that it does not happen again.
RESCUE
- Purpose - The purpose of this rescue plan is to establish College wide guidelines for responding to falls from height. This rescue plan is intended to reduce risks to an employee’s health after a fall arrest event. The rescue plan should also minimize the amount of at-risk behavior of the rescuer during the rescue attempt, and help to ensure that the rescue is conducted promptly in a safe and professional manner.
- Application
- This rescue plan applies to all locations where personnel are employed to work at height.
- The requirements of this rescue plan must be observed by all personnel involved in working at heights.
- This rescue plan must be reviewed or included in any job safety analysis or pre-task planning for activities that require working at heights.
- Definitions
- Rescue Plan: A strategy or procedure, planned in advance, to safely retrieve a person who has fallen from an elevated work surface and is suspended in a full body harness. This includes self-rescue or mechanically aided rescue.
- Self Rescue: An act or instance of an employee using his fall protection equipment to rescue him or herself.
- Mechanically Aided Rescue: A strategy or procedure, planned in advance, to safely retrieve a person who has fallen from an elevated work surface using mechanical means.
- Suspension Trauma: A serious medical condition that can lead to unconsciousness, injury or death, which can occur when a worker is suspended in a harness for too long after a fall.
- Prompt Rescue: The recommended goal for rescue subject contact is less than six minutes, per ANSI Z359.2-6.1.
- Rescue Responsibilities
- Employees:
- Must be trained in and familiar with the Fall Protection Policy.
- Must understand and be able to evaluate the risks associated with working at heights.
- Must be trained and competent in the use of fall protection equipment prior to conducting work at heights.
- Must report unsafe conditions or behaviors to the supervisor or lead worker (as designated by the Director of Facilities or their designee).
- Must be familiar with and understand the College’s rescue plan to provide prompt rescue in the event of an arrested fall event.
- Employees:
- Authorized Rescuer: Must be trained by a competent rescuer trainer before being exposed to a fall hazard or potential rescue application.
- Must be re-trained when the nature of the work, workplace, or methods of control or rescue change to an extent that prior training is no longer adequate.
- Must be trained on how to inspect, anchor, assemble and use the fall protection and rescue equipment used in locations where employees work. Training must include physical demonstrations by trainees.
- Training must include at least the following:
- Fall hazard recognition;
- Fall hazard elimination and control methods;
- Applicable fall protection and rescue regulations;
- How to use written fall protection and rescue procedures;
- Inspection of equipment components and systems before use.
-
- Refresher training must occur at least every two years for the authorized rescuer to stay current with fall protection and rescue educational requirements per ANSI.
- Must be evaluated by a competent rescuer or competent rescuer trainer at least annually to ensure competency of the duties assigned. This evaluation must include both a written examination and a physical demonstration of usage of all equipment the person is authorized to operate.
- Competent Rescuer:
- Must be trained by a competent rescuer trainer.
- Must be trained on how to inspect, anchor, assemble and use the fall protection and rescue equipment used in locations where employees work. Training must include physical demonstrations by trainees.
- Training must include use of all types of equipment and systems used in locations where rescues may be required, including inspection of systems prior to use, installation, component compatibility, descent control, secondary systems, packaging methods, dismantling, storage and the common hazards associated with each system and component.
- Training must include at least the following information:
- Fall hazard elimination and control methods;
- Applicable fall protection and rescue regulations;
- Assessment of fall hazards to determine rescue methods;
- Responsibilities of designated persons under this standard;
- Detailed inspection and recording of rescue equipment components and systems;
- Rescue systems assessment and determination of when a system is unsafe;
- Development of written fall protection rescue procedures;
- Selection and use of non-certified anchorages.
- Refresher training for Competent Person Rescuers must be conducted at least every year per ANSI.
- Rescue Procedure - A rescue plan must be identified for any job that requires work at height. The rescue plan must include consideration of the following rescue types and circumstances:
- Self Rescue - If the person working at heights has properly selected and used his or her fall protection equipment, 90% of workers will be able to perform a Self Rescue, which should include these steps:
- Climbing back up to the level from which he fell (from a few inches to 2-3 feet).
- Returning to the floor or ground to be evaluated for possible medical attention per OSHA.
- Removing all components of fall arrest system impacted by the fall event from service and documenting (bag and tag) the components with name, date and activity at time of fall and giving the equipment to management.
- Assisted Self Rescue with Mechanically Aided Hauling/Rope System - If self-rescue is not possible, then an Assisted Self Rescue will be needed. The following guidelines should be used during a mechanically aided rescue:
- A compliant rescue and descent device will be secured to an anchor that is rated for at least 3,000 lbs.
- The haul line may be swung over or lowered to the fallen worker, who will grab the rescue lifeline snap hook and secure it to the appropriate D-ring on his body support. A positive connection to the D-ring must be verified by one of the rescue team members.
- The rescue team will raise or lower the fallen employee to the appropriate work platform or ground and provide medical aid as required by OSHA.
- Remove all components of fall arrest system impacted by the fall event from service and document (bag and tag) the components with name, date and activity at time of fall and give the equipment to management.
- Mechanically Aided (unconscious) with hauling/rope system - If the worker’s injuries prevent the worker from attaching to the rescue system, both self-rescue and assisted self-rescue are not options, and a fully Assisted Rescue is necessary:
- A compliant rescue and descent device will be secured to an anchor that is rated for at least 3,000 lbs.
- A rescue team member must attach the haul line to the worker’s fall arrest system. This can be performed by accessing the fallen worker and then attaching the rescue system directly to a D-ring on the worker’s harness, or by using a rescue pole for the attachment. The rescue team could also attach a rescue grab to the lanyard or vertical lifeline.
- The rescue team must raise or lower the fallen worker to the appropriate work platform or ground and provide medical aid as required by OSHA.
- Remove all components of fall arrest system impacted by the fall event from service and document (bag and tag) the components with name, date and activity at time of fall and give the equipment to management.
- Assisted rescue with mechanically aided aerial lift - If another means of performing a fully Assisted Rescue is to use an aerial lift under the following guidelines:
- A rescuer will get into the aerial lift and make sure there is a second fall protection device, such as a shock absorbing lanyard or self-retracting lifeline available for the fallen worker.
- The aerial lift must be maneuvered into position (raised up underneath the fallen worker) so that the rescuer can perform the rescue.
- Attach the second lanyard or self-retracting lifeline in the aerial lift to the fallen worker.
- Disconnect the rescued worker from the impacted fall arrest equipment.
- Lower the worker to the ground and provide medical aid as required by OSHA.
- Remove all components of fall arrest system impacted by the fall event from service and document (bag and tag) the components with name, date and activity at time of fall and give the equipment to management
- Self Rescue - If the person working at heights has properly selected and used his or her fall protection equipment, 90% of workers will be able to perform a Self Rescue, which should include these steps:
Contact Us
Location
Our office is located on First Street in the Garden Level (lower level) of Main Hall in De Pere, Wis.
Campus Map
Hours of Operation
Monday-Friday
8 a.m.-4:30 p.m.
Phone: 920-403-3211
Fax: 920-403-3983
Email: hr@snc.edu