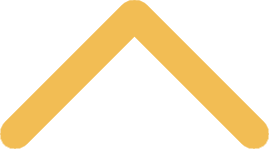
Safety: Hearing Conservation
Applies to: All faculty and staff working in areas considered a noise hazard
Purpose: The Hearing Conservation Program (HCP) outlines the types of environments that require safeguarding caused by excessive exposure to noise in the workplace and to assure compliance with applicable laws and regulations. The Hearing Conservation Program will identify the need (above 85dB for an 8 hour time weighted average) for general areas or entire buildings that will require noise monitoring, implementation of the program, baseline and annual audiograms for exposed employees and training as per the requirements of 29 CFR 1910.95.
Policy Owner: Human Resources
Revision Dates: December 2022
Policy
RESPONSIBILITIES
Departments - Each department is responsible for compliance with the criteria set forth in this program. They must ensure that all elements of this program and related procedures are implemented and followed.
Senior Benefits and Safety Specialist
- Assist in identifying all noise hazard and caution areas through monitoring.
- Assist in conducting initial noise exposure monitoring and re-monitoring annually, or whenever process/equipment changes take place.
- Assist in identifying those employees that should be included in the Hearing Conservation Program (HCP) by examining work environment and personnel monitoring results.
- Recommend engineering and administrative controls for reducing noise exposure, and review projects that may increase such exposures.
- Assist with setting up audiograms where required at the divisions.
- Assist with conducting or arranging employee training on an annual basis.
- Maintain all records relative to the HCP (e.g. noise monitoring results, hearing conservation employee list, and training records).
- Conduct annual inspections to evaluate the effectiveness of the HCP and to assure compliance.
- Review this policy annually to assure compliance with applicable laws and regulations.
- Review all projects that may increase noise exposures, and examine alternatives before introducing noise-producing systems into the plant.
- Implement and maintain engineering and/or administrative controls, as feasible, to reduce noise exposure.
- Provide Sr. Benefits and Safety Specialist with an updated listing of employees in the HCP on an annual basis if there are any changes.
- Ensure that baseline (within 6 months of hire or assignment) and annual audiograms are conducted by an authorized vendor.
- Assure employees are informed of their rights/obligations relating to HCP and properly trained.
- Assure that the employees are issued, and properly use, hearing protection in specified areas and during operations requiring its use.
- Post noise hazard and noise caution areas.
- Implement restrictions or re-assignments required by a certified audiologist for individuals experiencing hearing impairments or standard threshold shifts.
- Notify Sr. Benefits and Safety Specialist of any changes in production, procedures, equipment, or controls that may increase or decrease noise exposures.
- Participate in the audiometric and noise dosimeter surveillance procedures.
- Use personal protective equipment as instructed and in accordance with training received.
- Maintain personal protective equipment, and report any damage or loss to the supervisor.
- Attend HCP training, as scheduled.
- Report any malfunction of equipment or any other situation that may result in increased noise exposures to the supervisor.
DEFINITIONS
Impulse Noise - A sound that has a rise time of not more than 35 milliseconds to peak intensity and a duration of not more than 500 milliseconds to the time when the level is 30dBA below the peak. If the impulses recur at intervals of less than one second, they shall be considered as continuous sound.
Impact Noise – A special type of impulse noise in which sound is generated by two or more objects banging together. Thus, impact noise is always impulse noise, but impulse noise may not be impact noise - depending on the source of the noise.
Administrative Controls – Any procedure that limits daily exposure to noise by control of the work schedule. Examples of administrative controls include employee rotation, off-shift scheduling of high noise operations, etc.Engineering Controls – Any procedure other than administrative controls or personal protective equipment that reduces the sound level either at the source of noise or within the hearing zone to the employee. Examples of engineering controls are enclosures, mufflers, substitution of process or machine, etc.
Noise Hazard Area – Any area in which noise exposure is equal to or exceeds an 8-hour TWA sound level of 90dBA.
Noise Caution Area – Any area in which noise exposure is equal to or exceeds 85dBA, but is less than 90dBA on an 8-hour TWA.
Personal Protective Equipment – Hearing protective devices used to reduce employee noise exposure to less than 85dBA as an 8-hour TWA. There are basically three types of hearing protectors: earmuffs, ear plugs, and canal caps.
Audiometric Testing – The act of receiving an audiogram from an audiologist, otolaryngologist, or physician. An audiogram measures hearing levels as a function of frequency.
Monitoring – Measurement of noise exposures of levels by use of a sound level meter or a dosimeter.
Standard Threshold Shift – A change in hearing threshold relative to the baseline audiogram of an average of 10 dB or more at 2000, 3000, and 4000 Hz in either ear.
If a standard threshold shift is noted, repeat the audiogram approximately 2-3 weeks after the initial audiogram. This test can only be taken after 14 hours of noise free environment prior to the re-test.
Procedures
Monitoring
- Monitoring shall be done and/or repeated whenever a change in production, process, equipment or controls increases noise exposures to the extent that:
- Additional employees may be exposed at or above the action level; or
- The attenuation provided by hearing protectors being used by employees may be rendered inadequate to meet the requirements of paragraph (j) of this section.
- Within 21 days of the monitoring, any employee found to be exposed to noise in excess of 85dBA, based on an 8-hour TWA, will be informed of his/her exposure.
- Instruments used to measure noise levels will be properly calibrated.
- Monitoring conducted will comply with OSHA regulations described in 29 CFR 1910.95, Section D.
Audiometric Testing - Audiometric testing will be conducted on employees who have an occupational noise exposure as defined in this program, within 6 months of hire or assignment. Employees shall wear hearing protection until they are able to be tested.
Annual testing will be conducted thereafter for every employee participating in the HCP. There also may be an instance where an employee may need to be sent to a medical clinic for testing.
The audiometric testing will comply with OSHA regulations described in 29 CFR 1910.95, Section G and H. Each ear shall be tested separately with test frequencies at a minimum of 500, 1000, 2000, 3000, 4000 and 6000 Hz.
Any employee found to have a standard threshold shift (STS) will be notified in writing within 21 days of the test. The HR Safety Specialist and the appropriate departmental manager will be notified and will notify the employee(s) and discuss the significance of the standard threshold shift that they will be sent for re-testing within 30 days of notification. If the second test does not indicate an STS - the employee will be notified and no further testing is required until the next annual test is scheduled.
Hearing protection is re-evaluated in the event of a standard threshold shift. Unless a physician determines that the standard threshold shift is not work related or aggravated by occupational noise exposure, the employer shall ensure that employees already using hearing protectors shall be refitted and retrained in the use of hearing protectors and provided with hearing protectors offering greater attenuation if necessary.
Training - Employees in the HCP must receive training, upon entry into the program and annually thereafter, until no longer required to be in the HCP. Training will include the following:
- Effects of noise on hearing.
- Purpose of hearing protectors and advantages/disadvantages of the different types.
- Selection, use, fitting, attenuation characteristics, and care of hearing protectors.
- Purpose of audiometric testing and an explanation of the test procedures.
- Locations of noise hazard and noise caution areas and operations where hearing protection is required.
- Engineering and administrative controls in effect to reduce limit noise exposure.
- Rights and obligations of employees under OSHA regulations.
- Training will be conducted and recorded in Workday.
Engineering and Administrative Controls/Noise Abatement PlanEngineering and administrative controls will be used to reduce noise exposures to less than 90dBA, based on an 8-hour TWA, and 130dBA impact/impulse noise.
- If it is determined that engineering controls are not feasible to reduce noise exposure by modifying existing equipment to less than the 90dBA to 130dBA limits, the determination must be thoroughly documented and concurred by the Department Manager and Sr. Benefits and Safety Specialist. Then a Hearing Conservation Program shall be implemented.
- If noise cannot be reduced to permissible levels through feasible administrative or engineering controls, personal protective equipment shall be provided and used to reduce noise exposures to acceptable levels.
- If existing equipment is modified or new equipment is installed, noise monitoring will be done within 3 months of change in production, process, equipment or controls. If changes to equipment are over 90dBA, based on an 8-hour TWA, and 140dBA impact/impulse noise, engineering and administrative controls/noise abatement plan shall be implemented.
Personal Protective Equipment (PPE)
- Hearing protectors will be made available to employees at no cost.
- Employees shall be given the opportunity to select from a variety of suitable hearing protectors approved by the Department Manager and Sr. Benefits and Safety Specialist.
- Hearing protection must attenuate employee exposure at least to an 8-hour time-weighted average of 90dBA (See Appendix B in 29 CFR 1910.95). An example would be hearing protectors with an NRR rating of 33 – subtract 7 – divide by 2 and subtract that from the TWA measurement of the employee.
RECORDKEEPING – HCP records and documentation will be maintained as follows:
Sr. Benefits and Safety Specialist
- Area noise surveys and reports.
- Personal noise dosimeter results.
- Listing of personnel in HCP.
- Audiometric test results (kept for the length of employment).
- Medical restrictions relating to noise exposures and/or hearing impairments.
- Training through Workday.
Department Managers
- List, locate, and label noise hazard areas and equipment.
VISITORS & OTHER PERSONNEL - Visitors, contractors (personnel not under the direct supervision of the College), and other personnel will be required to comply with all administrative controls specified in this policy. Audiometric testing, fit testing, and other related restrictions will not apply. (Temporary employees under the direct supervision of the company will be included in the HCP policy, except for OSHA 29 CFR 1910.95 Section H.)
PROGRAM EVALUATION - The Sr. Benefits and Safety Specialist will conduct periodic evaluations of the workplace to ensure that the provisions of this program are being implemented. The evaluation will include regular consultations with employees who utilize PPE, their supervisors, site inspections and review of records. Identified problems will be noted and addressed by the Sr. Benefits and Safety Specialist. These findings will be reported to management, and the report will list plans to correct deficiencies and target dates for the implementations of those corrections.
DOCUMENTATION AND RECORDKEEPING - Copies of training and record of training will be retained in Workday. These records will be updated as new employees are trained and as existing employees receive refresher training.
PROGRAM REVIEW AND UPDATE - This policy shall be reviewed and updated on an annual basis or sooner if necessary.
Policy
RESPONSIBILITIES
Departments - Each department is responsible for compliance with the criteria set forth in this program. They must ensure that all elements of this program and related procedures are implemented and followed.
Senior Benefits and Safety Specialist
- Assist in identifying all noise hazard and caution areas through monitoring.
- Assist in conducting initial noise exposure monitoring and re-monitoring annually, or whenever process/equipment changes take place.
- Assist in identifying those employees that should be included in the Hearing Conservation Program (HCP) by examining work environment and personnel monitoring results.
- Recommend engineering and administrative controls for reducing noise exposure, and review projects that may increase such exposures.
- Assist with setting up audiograms where required at the divisions.
- Assist with conducting or arranging employee training on an annual basis.
- Maintain all records relative to the HCP (e.g. noise monitoring results, hearing conservation employee list, and training records).
- Conduct annual inspections to evaluate the effectiveness of the HCP and to assure compliance.
- Review this policy annually to assure compliance with applicable laws and regulations.
- Review all projects that may increase noise exposures, and examine alternatives before introducing noise-producing systems into the plant.
- Implement and maintain engineering and/or administrative controls, as feasible, to reduce noise exposure.
- Provide Sr. Benefits and Safety Specialist with an updated listing of employees in the HCP on an annual basis if there are any changes.
- Ensure that baseline (within 6 months of hire or assignment) and annual audiograms are conducted by an authorized vendor.
- Assure employees are informed of their rights/obligations relating to HCP and properly trained.
- Assure that the employees are issued, and properly use, hearing protection in specified areas and during operations requiring its use.
- Post noise hazard and noise caution areas.
- Implement restrictions or re-assignments required by a certified audiologist for individuals experiencing hearing impairments or standard threshold shifts.
- Notify Sr. Benefits and Safety Specialist of any changes in production, procedures, equipment, or controls that may increase or decrease noise exposures.
- Participate in the audiometric and noise dosimeter surveillance procedures.
- Use personal protective equipment as instructed and in accordance with training received.
- Maintain personal protective equipment, and report any damage or loss to the supervisor.
- Attend HCP training, as scheduled.
- Report any malfunction of equipment or any other situation that may result in increased noise exposures to the supervisor.
DEFINITIONS
Impulse Noise - A sound that has a rise time of not more than 35 milliseconds to peak intensity and a duration of not more than 500 milliseconds to the time when the level is 30dBA below the peak. If the impulses recur at intervals of less than one second, they shall be considered as continuous sound.
Impact Noise – A special type of impulse noise in which sound is generated by two or more objects banging together. Thus, impact noise is always impulse noise, but impulse noise may not be impact noise - depending on the source of the noise.
Administrative Controls – Any procedure that limits daily exposure to noise by control of the work schedule. Examples of administrative controls include employee rotation, off-shift scheduling of high noise operations, etc.Engineering Controls – Any procedure other than administrative controls or personal protective equipment that reduces the sound level either at the source of noise or within the hearing zone to the employee. Examples of engineering controls are enclosures, mufflers, substitution of process or machine, etc.
Noise Hazard Area – Any area in which noise exposure is equal to or exceeds an 8-hour TWA sound level of 90dBA.
Noise Caution Area – Any area in which noise exposure is equal to or exceeds 85dBA, but is less than 90dBA on an 8-hour TWA.
Personal Protective Equipment – Hearing protective devices used to reduce employee noise exposure to less than 85dBA as an 8-hour TWA. There are basically three types of hearing protectors: earmuffs, ear plugs, and canal caps.
Audiometric Testing – The act of receiving an audiogram from an audiologist, otolaryngologist, or physician. An audiogram measures hearing levels as a function of frequency.
Monitoring – Measurement of noise exposures of levels by use of a sound level meter or a dosimeter.
Standard Threshold Shift – A change in hearing threshold relative to the baseline audiogram of an average of 10 dB or more at 2000, 3000, and 4000 Hz in either ear.
If a standard threshold shift is noted, repeat the audiogram approximately 2-3 weeks after the initial audiogram. This test can only be taken after 14 hours of noise free environment prior to the re-test.
Procedures
Monitoring
- Monitoring shall be done and/or repeated whenever a change in production, process, equipment or controls increases noise exposures to the extent that:
- Additional employees may be exposed at or above the action level; or
- The attenuation provided by hearing protectors being used by employees may be rendered inadequate to meet the requirements of paragraph (j) of this section.
- Within 21 days of the monitoring, any employee found to be exposed to noise in excess of 85dBA, based on an 8-hour TWA, will be informed of his/her exposure.
- Instruments used to measure noise levels will be properly calibrated.
- Monitoring conducted will comply with OSHA regulations described in 29 CFR 1910.95, Section D.
Audiometric Testing - Audiometric testing will be conducted on employees who have an occupational noise exposure as defined in this program, within 6 months of hire or assignment. Employees shall wear hearing protection until they are able to be tested.
Annual testing will be conducted thereafter for every employee participating in the HCP. There also may be an instance where an employee may need to be sent to a medical clinic for testing.
The audiometric testing will comply with OSHA regulations described in 29 CFR 1910.95, Section G and H. Each ear shall be tested separately with test frequencies at a minimum of 500, 1000, 2000, 3000, 4000 and 6000 Hz.
Any employee found to have a standard threshold shift (STS) will be notified in writing within 21 days of the test. The HR Safety Specialist and the appropriate departmental manager will be notified and will notify the employee(s) and discuss the significance of the standard threshold shift that they will be sent for re-testing within 30 days of notification. If the second test does not indicate an STS - the employee will be notified and no further testing is required until the next annual test is scheduled.
Hearing protection is re-evaluated in the event of a standard threshold shift. Unless a physician determines that the standard threshold shift is not work related or aggravated by occupational noise exposure, the employer shall ensure that employees already using hearing protectors shall be refitted and retrained in the use of hearing protectors and provided with hearing protectors offering greater attenuation if necessary.
Training - Employees in the HCP must receive training, upon entry into the program and annually thereafter, until no longer required to be in the HCP. Training will include the following:
- Effects of noise on hearing.
- Purpose of hearing protectors and advantages/disadvantages of the different types.
- Selection, use, fitting, attenuation characteristics, and care of hearing protectors.
- Purpose of audiometric testing and an explanation of the test procedures.
- Locations of noise hazard and noise caution areas and operations where hearing protection is required.
- Engineering and administrative controls in effect to reduce limit noise exposure.
- Rights and obligations of employees under OSHA regulations.
- Training will be conducted and recorded in Workday.
Engineering and Administrative Controls/Noise Abatement PlanEngineering and administrative controls will be used to reduce noise exposures to less than 90dBA, based on an 8-hour TWA, and 130dBA impact/impulse noise.
- If it is determined that engineering controls are not feasible to reduce noise exposure by modifying existing equipment to less than the 90dBA to 130dBA limits, the determination must be thoroughly documented and concurred by the Department Manager and Sr. Benefits and Safety Specialist. Then a Hearing Conservation Program shall be implemented.
- If noise cannot be reduced to permissible levels through feasible administrative or engineering controls, personal protective equipment shall be provided and used to reduce noise exposures to acceptable levels.
- If existing equipment is modified or new equipment is installed, noise monitoring will be done within 3 months of change in production, process, equipment or controls. If changes to equipment are over 90dBA, based on an 8-hour TWA, and 140dBA impact/impulse noise, engineering and administrative controls/noise abatement plan shall be implemented.
Personal Protective Equipment (PPE)
- Hearing protectors will be made available to employees at no cost.
- Employees shall be given the opportunity to select from a variety of suitable hearing protectors approved by the Department Manager and Sr. Benefits and Safety Specialist.
- Hearing protection must attenuate employee exposure at least to an 8-hour time-weighted average of 90dBA (See Appendix B in 29 CFR 1910.95). An example would be hearing protectors with an NRR rating of 33 – subtract 7 – divide by 2 and subtract that from the TWA measurement of the employee.
RECORDKEEPING – HCP records and documentation will be maintained as follows:
Sr. Benefits and Safety Specialist
- Area noise surveys and reports.
- Personal noise dosimeter results.
- Listing of personnel in HCP.
- Audiometric test results (kept for the length of employment).
- Medical restrictions relating to noise exposures and/or hearing impairments.
- Training through Workday.
Department Managers
- List, locate, and label noise hazard areas and equipment.
VISITORS & OTHER PERSONNEL - Visitors, contractors (personnel not under the direct supervision of the College), and other personnel will be required to comply with all administrative controls specified in this policy. Audiometric testing, fit testing, and other related restrictions will not apply. (Temporary employees under the direct supervision of the company will be included in the HCP policy, except for OSHA 29 CFR 1910.95 Section H.)
PROGRAM EVALUATION - The Sr. Benefits and Safety Specialist will conduct periodic evaluations of the workplace to ensure that the provisions of this program are being implemented. The evaluation will include regular consultations with employees who utilize PPE, their supervisors, site inspections and review of records. Identified problems will be noted and addressed by the Sr. Benefits and Safety Specialist. These findings will be reported to management, and the report will list plans to correct deficiencies and target dates for the implementations of those corrections.
DOCUMENTATION AND RECORDKEEPING - Copies of training and record of training will be retained in Workday. These records will be updated as new employees are trained and as existing employees receive refresher training.
PROGRAM REVIEW AND UPDATE - This policy shall be reviewed and updated on an annual basis or sooner if necessary.
Contact Us
Location
Our office is located on First Street in the Garden Level (lower level) of Main Hall in De Pere, Wis.
Campus Map
Hours of Operation
Monday-Friday
8 a.m.-4:30 p.m.
Phone: 920-403-3211
Fax: 920-403-3983
Email: hr@snc.edu